Sheet Metal Fabrication
Our Expert Machinery
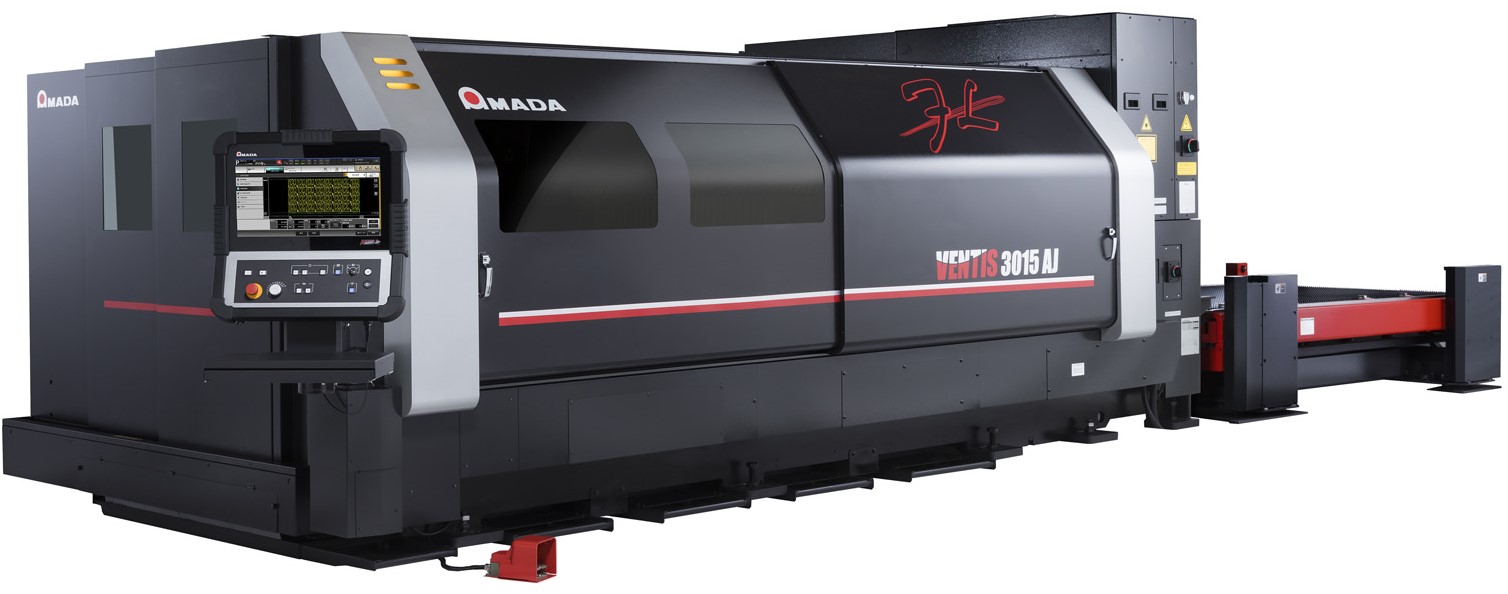
Ventis-AJ Fibre Laser
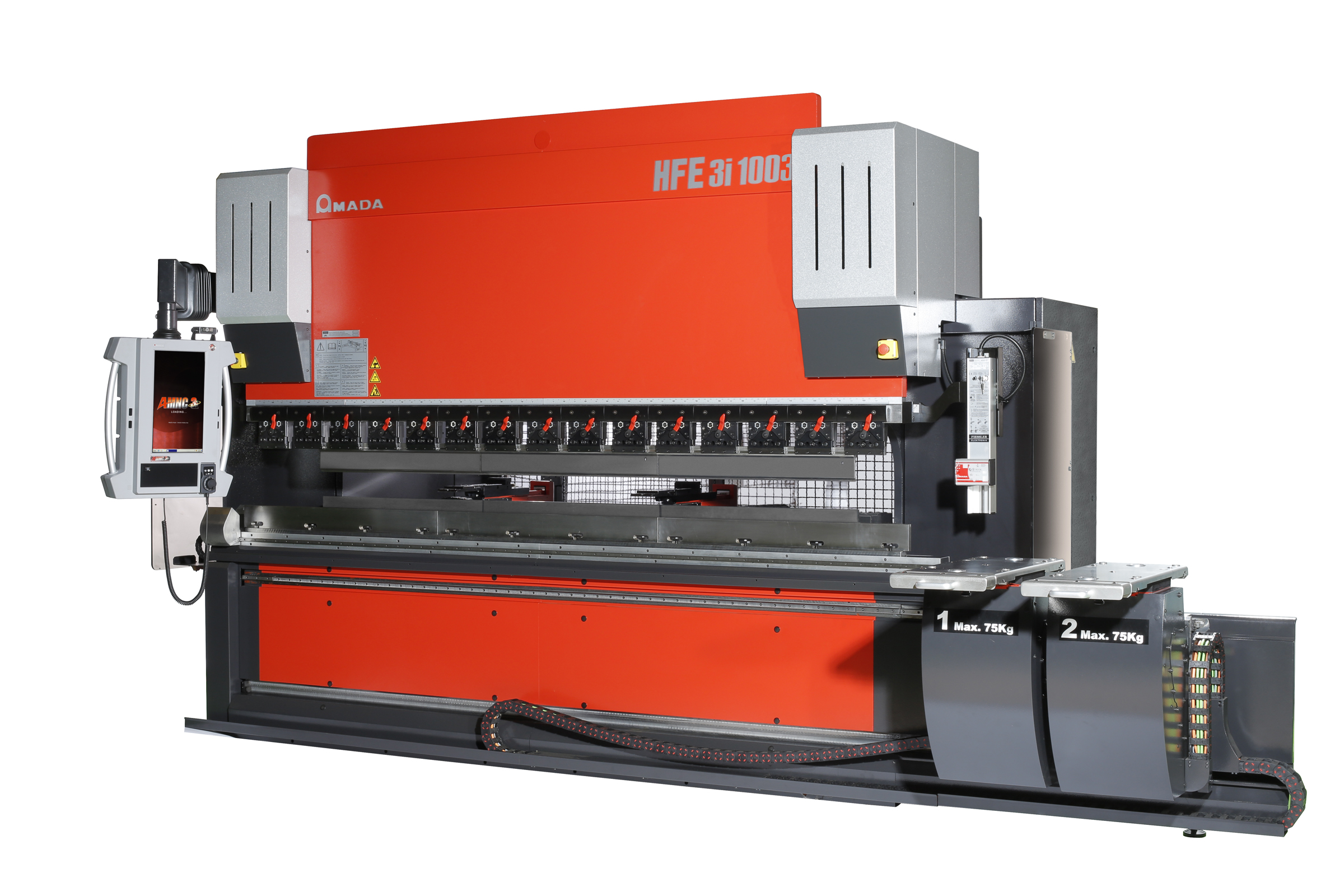
AMADA HFE3i
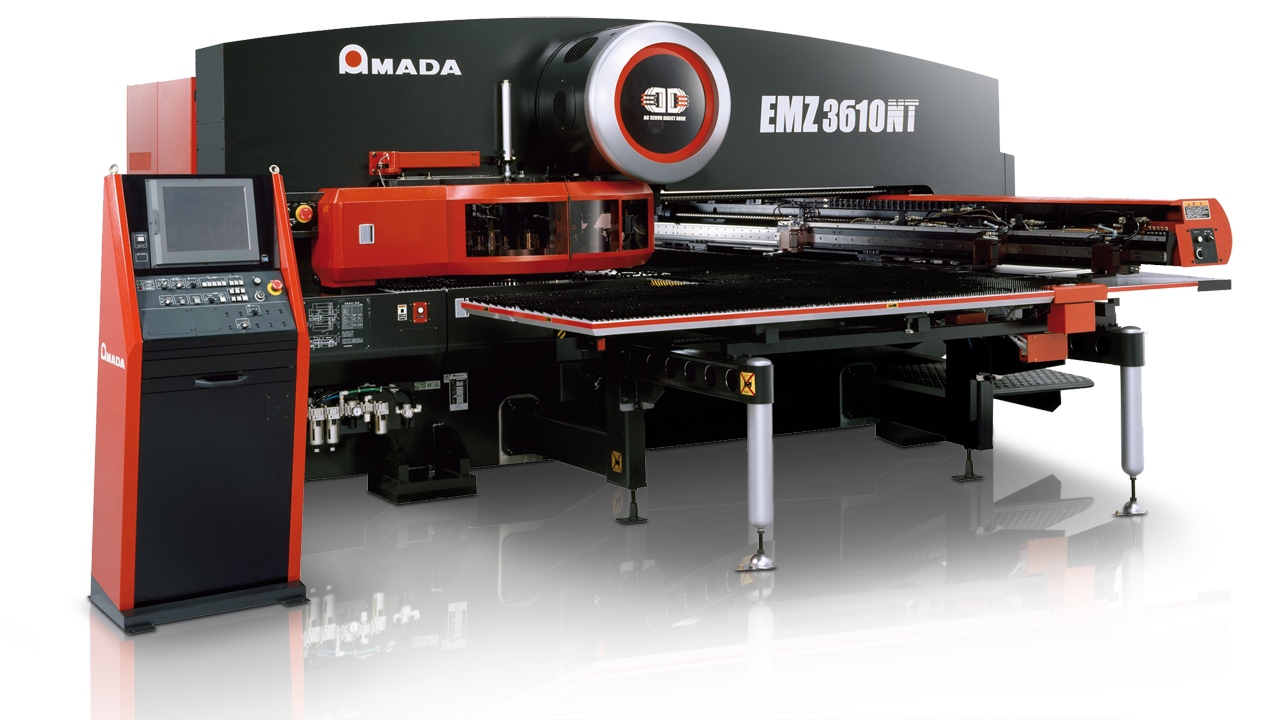
AMADA EMX-3610
Our Capabilities
Fabrication Services We Offer
- Laser Cutting
- Powder Coating
- Finishing
- Welding and Spot Welding
- Bending and Forming
- Product Assembly
- Design and Prototyping
- CNC Metal Punching
Metal Thickness
- Mild Steel: 0.5mm-25mm
- Stainless Steel: 0.5mm-20mm
- Aluminium: 0.5mm-16mm
- Brass: 0.5mm-10mm
- Copper: 0.5mm-8mm
Sheet Sizes
- Up to 3000 x 1500mm
Sectors We Can Provide Metal Fabrication Services For
Greengate Metal Components provides reliable and high-quality sheet metal fabrication services, tailored to meet the diverse needs of a range of businesses, such as:
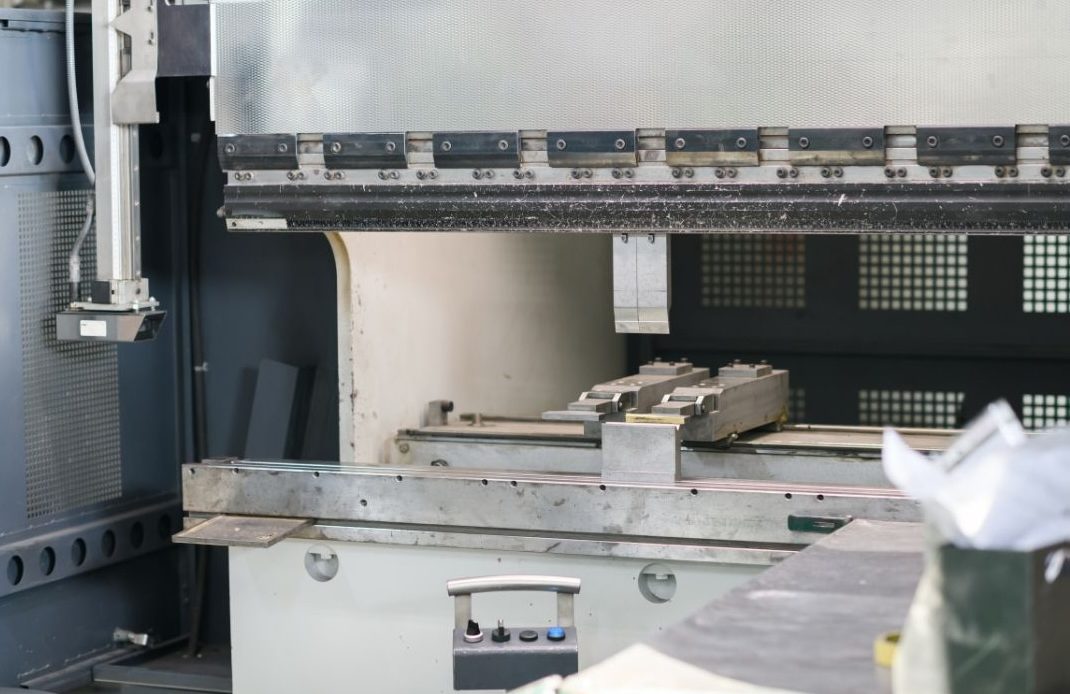
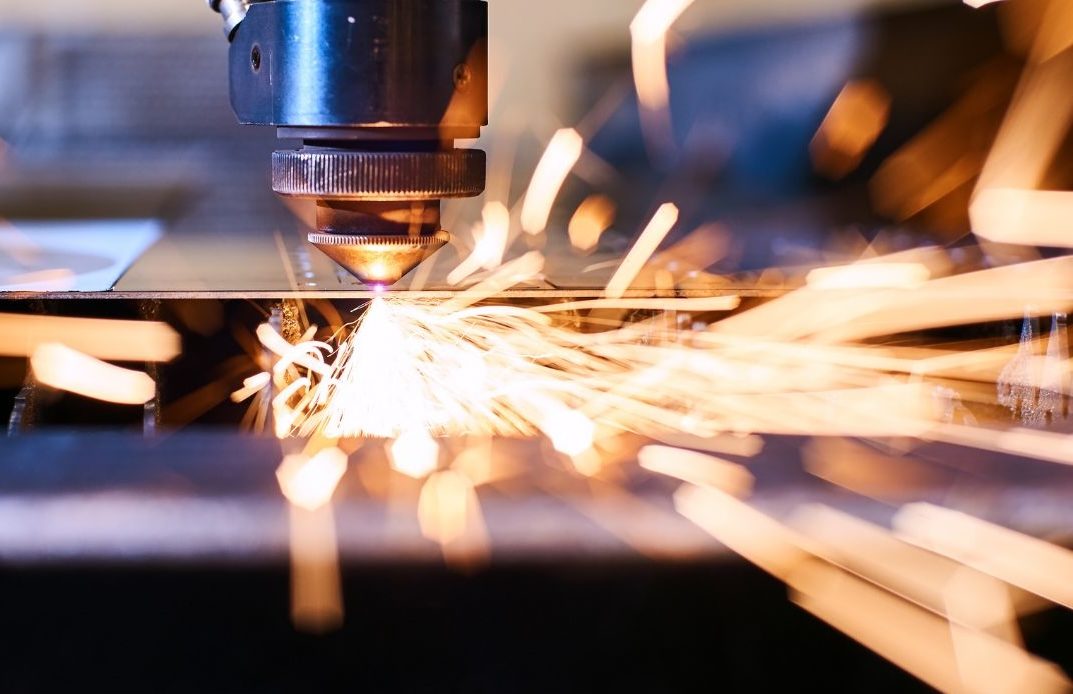
CNC Metal Laser Cutting
At Greengate Metal Components, our CNC metal laser cutting services offer exceptional precision, speed, and efficiency for a wide variety of fabrication needs. Using advanced laser technology, we can cut complex shapes and fine details with minimal waste and high repeatability.
Our skilled team ensures consistent quality and fast turnaround times, whether for prototypes or large-scale production. We work with various metals and thicknesses, delivering reliable results that meet the exact specifications of each project.
CNC Metal Punching
At Greengate Metal Components, our CNC metal punching services offer fast, accurate, and cost-effective solutions for producing complex metal parts.
Using advanced CNC punching machines, we can handle a wide range of materials and thicknesses with exceptional precision. This technology enables high-speed production with minimal waste, making it ideal for both small and large batch runs.
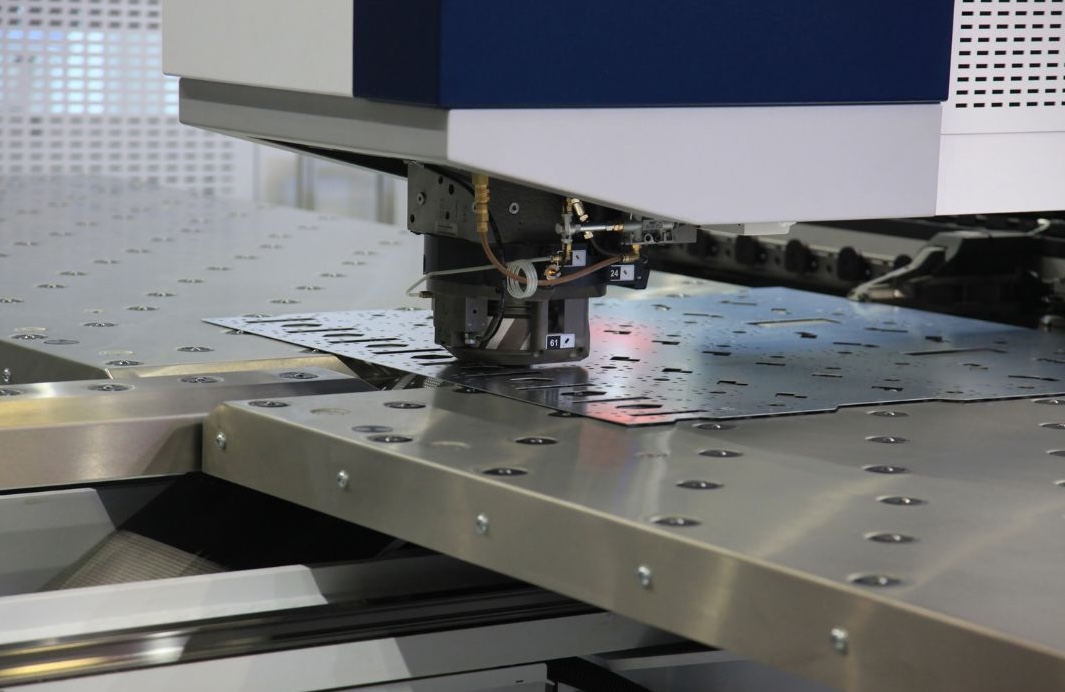
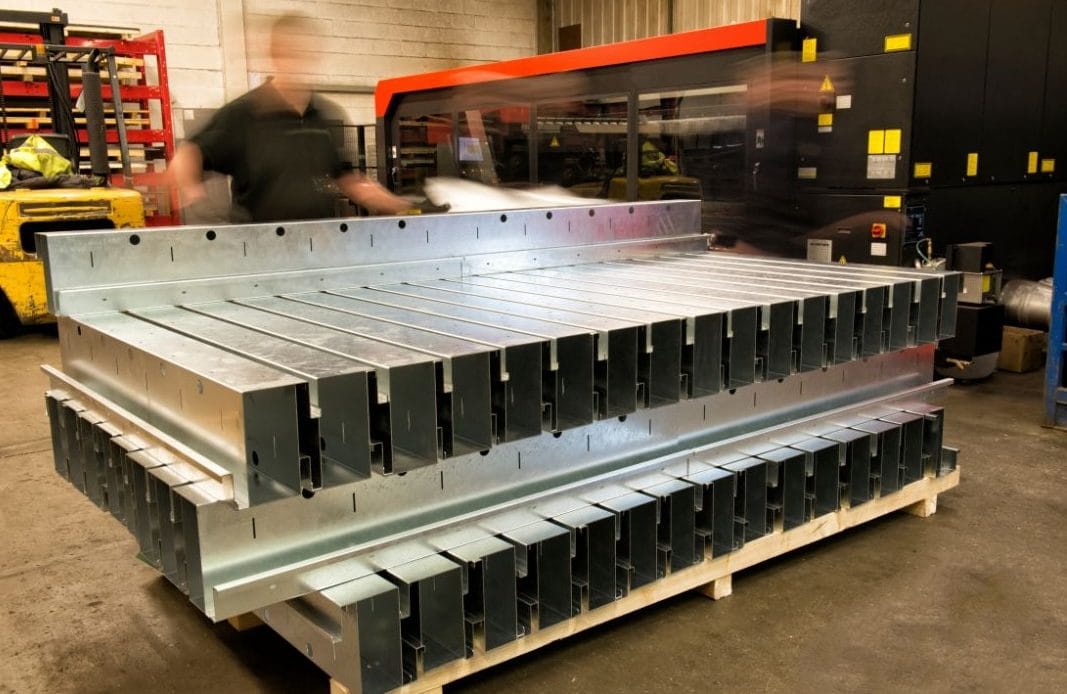
Sheet Metal Assembly
Our sheet metal assembly services are designed to deliver fully integrated, ready-to-use components that meet exact specifications.
We combine expert fabrication with skilled assembly techniques, including welding, fastening, and finishing, to ensure each product is precise and reliable. Our team works closely with clients to streamline production, reduce lead times, and maintain the highest quality standards.
Metal Welding
We offer professional metal welding services as part of our fabrication capabilities. Our skilled welders use advanced techniques and equipment to ensure strong, precise, and clean welds across a variety of metals.
Whether for structural frameworks or detailed component assembly, we maintain high standards of quality and consistency. With a focus on durability and accuracy, our welding services support both small and large-scale projects, tailored to meet the specific requirements of each client.
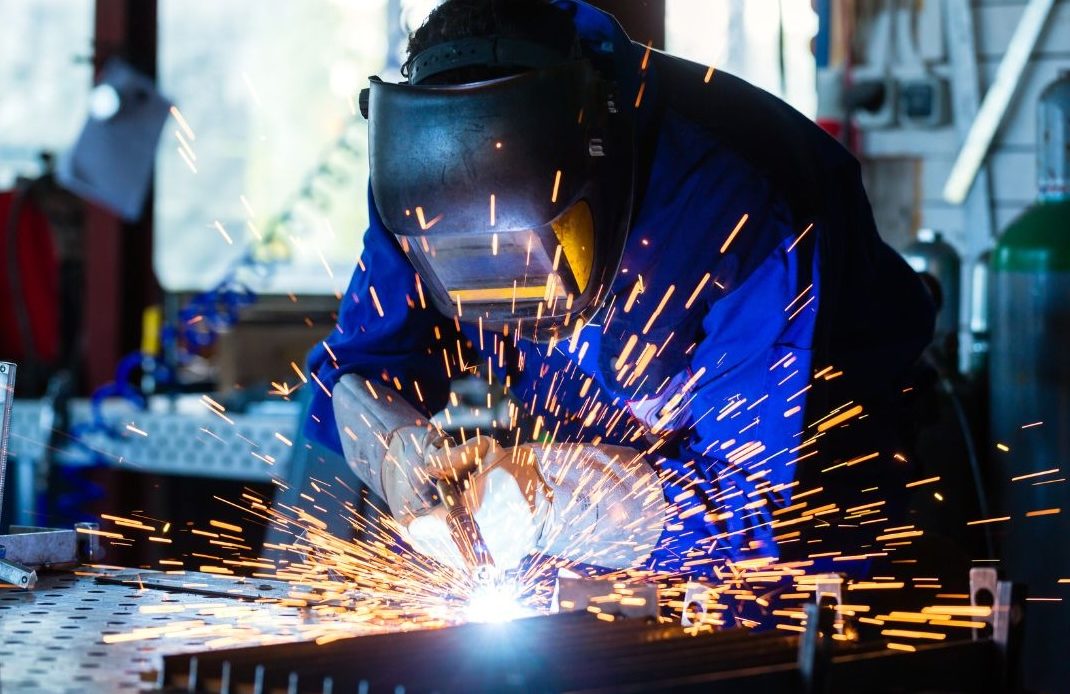
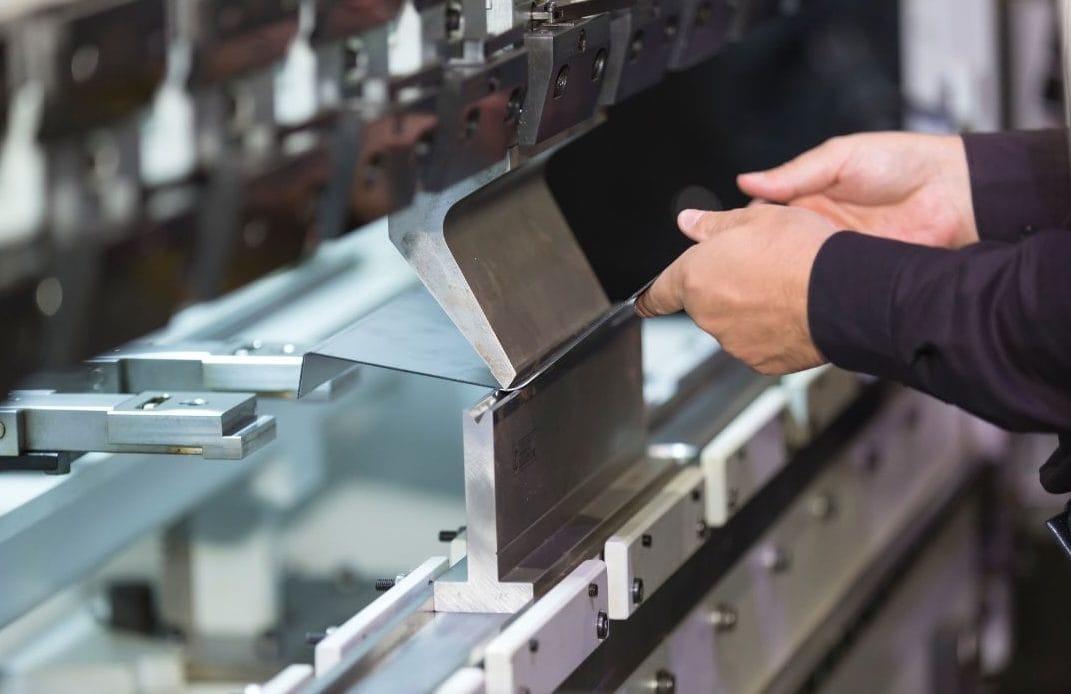
Metal Bending and Forming
At Greengate Metal Components, our metal bending and forming services combine precision, efficiency, and versatility to meet a wide range of project requirements. Using advanced CNC press brakes and skilled technicians, we can accurately shape sheet metal into complex forms with tight tolerances.
Our expertise in metal forming allows us to support custom designs, helping clients achieve optimal functionality and performance.
Metal Design and Prototyping
At Greengate Metal Components, our metal design and prototyping services ensure your ideas are brought to life with precision and efficiency. Using advanced CAD software and engineering expertise, we work closely with clients to develop accurate prototypes that meet functional and aesthetic requirements.
This process allows for thorough testing, refinement, and validation before full-scale production, reducing risk and saving time.
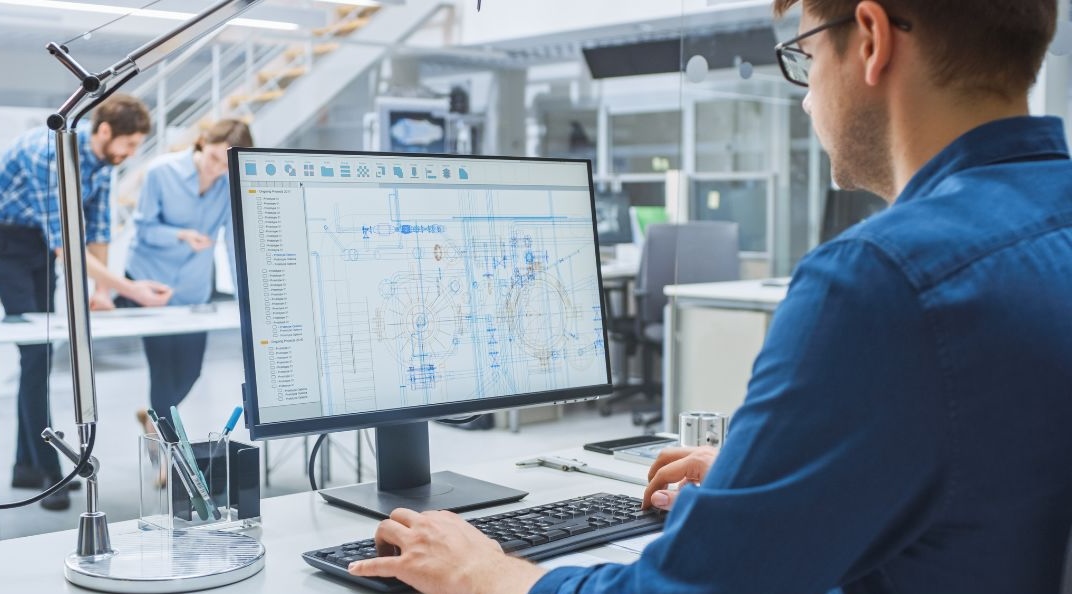
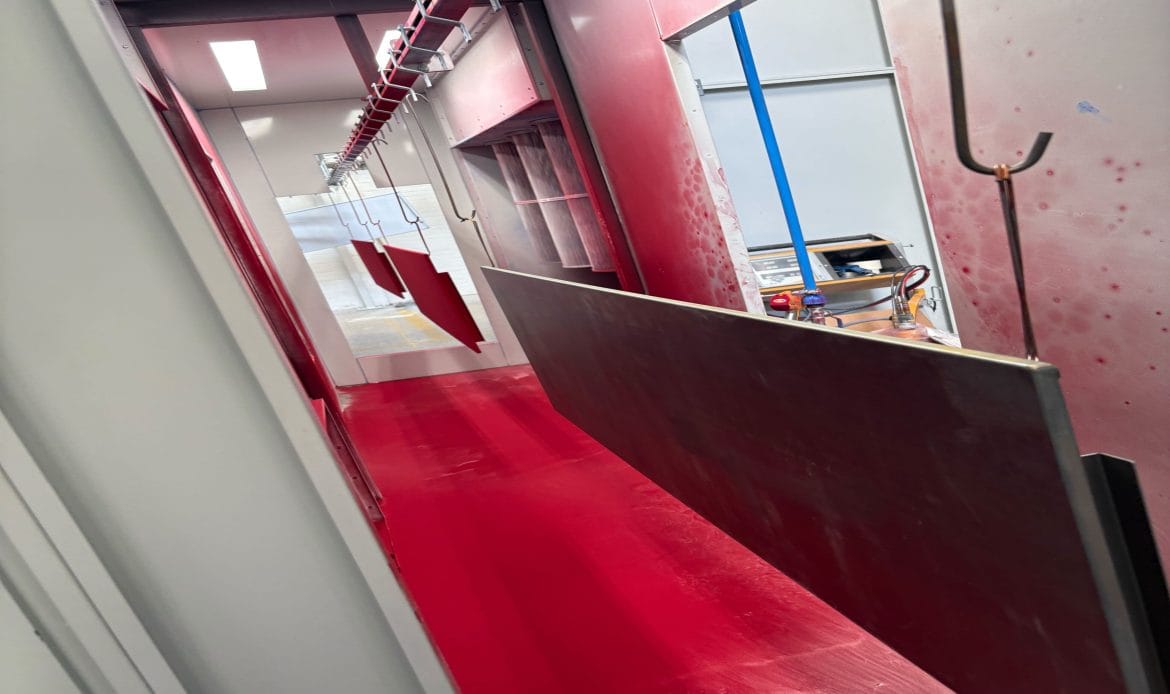
Metal Powder Coating
We offer professional metal powder coating services designed to enhance durability, appearance, and corrosion resistance.
Our advanced powder coating process delivers a smooth, uniform finish that adheres exceptionally well to metal surfaces, ensuring long-lasting performance. Available in a wide range of colours and textures, our coatings are ideal for both functional and aesthetic applications.