Getting things right early on – that’s really what metal fabrication prototyping is all about. It gives engineering and design teams the room to fine-tune, test, and push their ideas before committing to full production. Whether it’s sheet metal prototyping for a new product line or experimenting with fit and function using CNC prototyping, this early stage often shapes the entire project.
So, it’s not just about checking boxes – it’s more about avoiding delays, cutting back on waste, and delivering parts that actually work first time. And if you’re weighing up fabrication partners, the ability to handle prototyping for quality control can be a pretty strong indicator of technical know-how.
What is Metal Prototyping?
In short, metal fabrication prototyping is where design plans stop being theoretical and start getting practical. It’s the process of building a working version – or a close approximation – of a component before full-scale production begins. For design engineers, especially those creating unique or low-volume builds, it’s a chance to bridge the gap between screen and shop floor.
This isn’t about mass output. It’s more about precision – often one-off or short-run pieces – shaped and tested to see how well they perform in the real world. That’s why sheet metal prototyping often gets used in early development, especially for enclosures, brackets, and custom assemblies.
Depending on the complexity, these prototypes might be 3D-printed, CNC-machined, or manually assembled – all classed as physical metal prototypes. One way or another, they reveal problems early, help avoid miscommunication, and give clients something tangible to evaluate.
The benefits of metal fabrication prototyping? More accuracy, fewer surprises, and smoother production once things scale up.
Types of Prototyping in Metal Fabrication
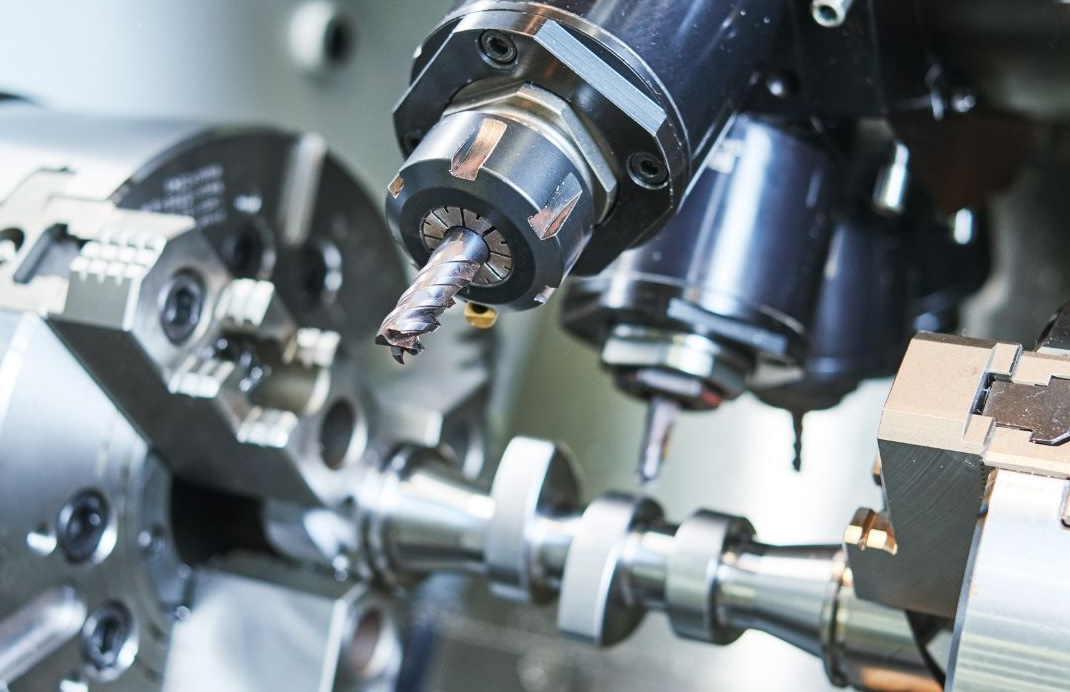
Digital Prototyping
Digital metal prototyping doesn’t involve any cutting or bending – not yet, anyway. Instead, it relies on CAD models and simulation tools to test how a part might behave, long before any metal gets touched. For engineers, this offers a way to tweak dimensions, test tolerances, and check material stress points in a digital space.
This approach suits complex designs where accuracy matters more than speed. Say you’re working on a high-precision assembly; digital testing helps flag potential clashes, weak points, or fabrication concerns early on.
And it’s not just about precision. Digital models help reduce material waste too – if something’s off, you fix it in the file, not in the workshop. So, while it doesn’t replace physical trials, digital metal prototyping gives you a much cleaner starting point for the hands-on stages that follow.
Physical Prototypes
This is where ideas take a more hands-on shape. With physical metal prototypes, you’re looking at real-world samples made from the actual materials intended for the final part. That might mean CNC-milled brackets, folded sheet panels, or even hand-finished components – it depends on what’s being tested.
CNC prototyping plays a big role here. It gives engineers the accuracy they need to confirm that a part fits, moves, or behaves as expected. It also helps iron out assembly challenges before they become real production headaches.
There’s also a bit of reassurance that comes from holding a prototype. Stakeholders can physically inspect it, test it, and give feedback with a lot more clarity than a digital render ever could.
So, whether it’s one component or a small batch, physical metal prototypes tend to be the step that gives your design some solid, tangible momentum.
Rapid Prototyping
If speed’s the priority, rapid prototyping in fabrication is often the go-to. This approach blends advanced tech like high-speed CNC and 3D printing to create testable parts in a fraction of the time it used to take.
In a way, it’s the fast-forward button for early-stage product development. You get physical parts – sometimes even within 24 to 48 hours – that let your team make real-world assessments almost instantly. For complex or iterative designs, this can seriously shorten the gap between concept and production.
Rapid prototypes aren’t always production-ready, but they’re usually “real enough” to guide changes, test form and fit, or show to decision-makers. It’s that early feedback – fast and fairly low cost – that makes metal fabrication prototyping so much more agile when this method is part of the mix.
Prototyping Methods Compared
- Digital Prototyping:
- Great for design validation and simulation
- Reduces material waste
- Speeds up pre-production decision-making
- Physical Prototypes:
- Ideal for tactile testing and hands-on evaluation
- Suits stakeholder reviews and functional checks
- Strong alignment with final materials and tolerances
- Rapid Prototyping:
- Best for fast turnaround and early testing
- Helps accelerate iterations and decision cycles
- Supports proof-of-concept development at pace
How Prototyping Impacts Quality Control in Metal Fabrication
Spotting issues early is cheaper than fixing them later. That’s one of the quieter benefits of sheet metal fabrication prototyping – it catches design flaws before they hit the production line. Whether it’s a tolerance mismatch or a poor material choice, prototypes shine a light on problems that don’t always show up in drawings.
Prototyping for quality control works on multiple levels. Fit testing, for example, confirms whether parts slot together correctly in real-world use. That’s something even the best CAD software might miss. CNC-machined samples – often used in CNC prototyping – allow for extremely precise assessments, right down to fractions of a millimetre.
Then there’s user feedback. In projects where components interact with people – control panels, housings, brackets – a physical prototype gives end users a chance to weigh in early, often saving a few painful revisions down the line.
On top of that, prototyping helps teams stay aligned with regulatory and industry standards. If a part needs to meet safety codes or structural guidelines, confirming that during prototyping rather than post-production avoids rework, delays, and extra cost.
For teams focused on getting parts right the first time, the benefits of metal fabrication prototyping speak for themselves. It helps sharpen designs, smooth out production hiccups, and reduce the risk of costly surprises.
Whether through digital, physical, or rapid methods, prototyping has become a useful checkpoint for both design precision and manufacturing quality. It’s not just about speed or testing – it’s a way to build confidence in what comes next.Want to explore what that could look like for your next project? Contact us to speak with our team at Greengate Metal Components to find out more.