Sheet metal fabrication is at the centre of modern manufacturing, and provides a reliable method for creating precise and adaptable components across a broad spectrum of applications. This process turns flat metal sheets into functional, durable, and visually appealing products, serving industries ranging from aerospace to construction, automotive, and consumer goods. Whether producing lightweight airframe components or structural supports, sheet metal fabrication combines precision and efficiency to meet the unique demands of diverse sectors.
The sheet metal fabrication process involves a series of carefully executed steps, each contributing to the creation of high-quality end products. These stages include design and prototyping, cutting processes, forming, welding, assembly, and finishing. These allow manufacturers to develop solutions that balance strength, functionality, and aesthetic appeal. With advancements in technology, such as CNC machinery and advanced finishing techniques, sheet metal fabrication now offers a high level of accuracy and consistency, and products meet even the most stringent requirements.
This guide looks at each step of the fabrication process, shedding light on the craftsmanship, expertise, and technology that power these processes. Whether you’re an engineer, product designer, or industry professional, this comprehensive overview will provide valuable insights into the benefits and applications of sheet metal fabrication for your projects.
Design and Prototyping
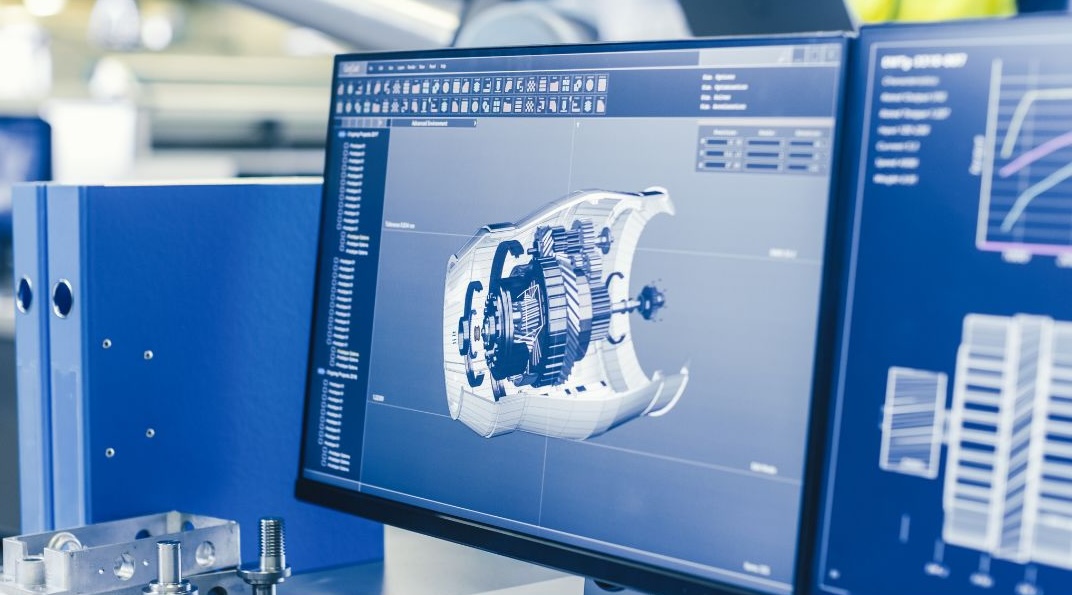
Design and prototyping are the base stages of sheet metal fabrication, turning initial concepts into practical, production-ready solutions. These steps set the groundwork for efficient manufacturing, this means that the final product matches with both functional and aesthetic objectives. A well-executed design and prototyping phase reduces errors, saves costs, and improves overall production timelines.
Collaboration is central to this process. Engineers and designers work closely to develop detailed computer-aided design (CAD) models, which act as the blueprint for the entire fabrication workflow. These models include precise specifications such as dimensions, tolerances, and material requirements so that the design is optimised for manufacturability. CAD software also allows for rapid iterations, enabling teams to adapt to evolving project needs or identify potential improvements before production begins.
Prototyping bridges the gap between design and full-scale production by creating physical models of the component or product. These prototypes provide an opportunity to test the design, identify issues, and refine details. Techniques such as 3D printing or CNC machining are often employed during prototyping to provide accuracy and speed. This iterative approach gives manufacturers the confidence to proceed with production, knowing the design has been thoroughly validated. Ultimately, a strong design and prototyping phase drives the success of the entire fabrication process.
Cutting
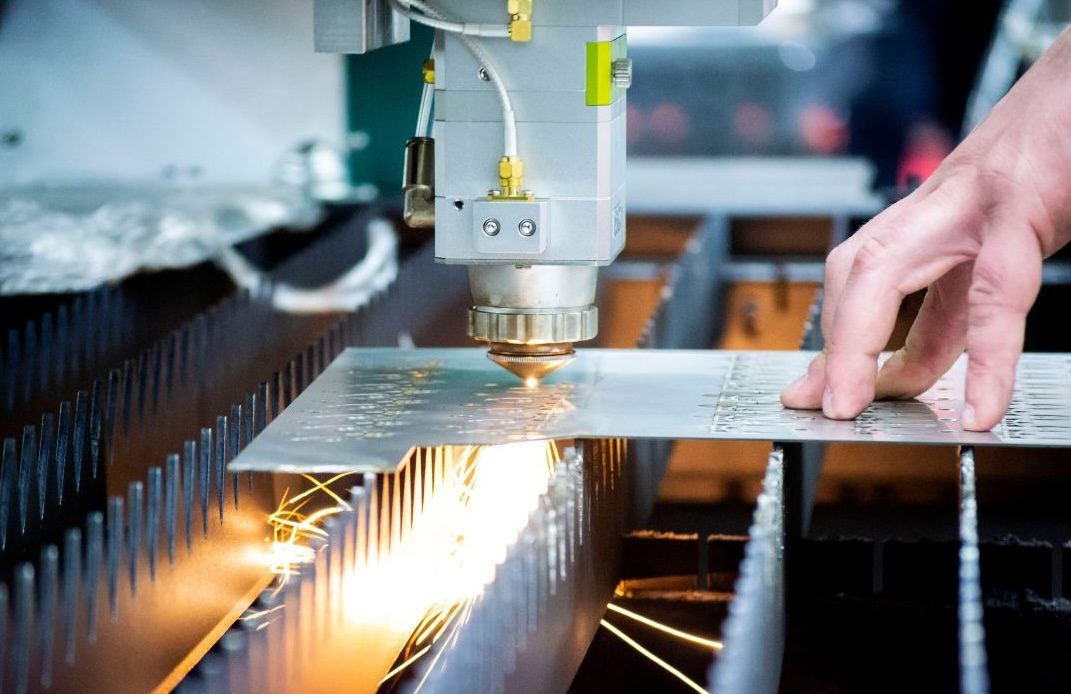
Cutting is the first step in changing raw sheet metal into usable components. Precision at this stage is needed to achieve smooth assembly and minimising material waste. Modern cutting techniques rely on advanced machinery to produce accurate and repeatable results, adapted to specific project requirements and designs.
The industry has moved beyond traditional methods like shearing, focusing on efficient and versatile technologies such as CNC laser cutting, CNC punching, and plasma cutting. These techniques allow manufacturers to work with a wide range of materials and create intricate designs with high levels of accuracy. By setting the foundation for subsequent processes, cutting makes sure the rest of the fabrication workflow proceeds efficiently.
CNC Laser Cutting
CNC laser cutting is one of the most advanced methods available for sheet metal fabrication. A high-powered laser beam precisely cuts intricate patterns or detailed designs, making it invaluable for industries requiring complex geometries, such as electronics, aerospace, and automotive.
Laser cutting delivers smooth edges, reduces material waste, and operates at high speeds, offering substantial cost savings for large projects. This method is effective for thin metals like stainless steel or aluminium but can also handle thicker materials with appropriate settings. CNC automation enables high consistency across production runs while accommodating detailed customisation for unique designs.
CNC Punching
CNC punching offers an efficient solution for creating holes, slots, or cut-outs in sheet metal. Using a programmed punch and die, this technique works exceptionally well for repetitive patterns and high-volume production.
This method is particularly effective for parts such as enclosures, panels, and brackets, where speed and accuracy are essential. It supports a variety of materials and thicknesses, making it suitable for many industries. Additionally, CNC punching can combine multiple punches in a single process, allowing for intricate designs and high repeatability. It is widely used in projects that require scalability without compromising on quality.
Plasma Cutting
Plasma cutting is a dependable option for processing thicker and more durable metals. It employs ionised gas to create a high-temperature plasma arc, enabling it to cut through materials like steel with ease and precision.
Widely used in industries such as construction and heavy machinery, plasma cutting excels in applications requiring thick material processing. Its ability to handle these materials without sacrificing accuracy makes it a preferred solution for structural components and heavy-duty projects. Plasma cutting also works well for repairing or modifying existing parts, making it a flexible option in various manufacturing settings.
Forming
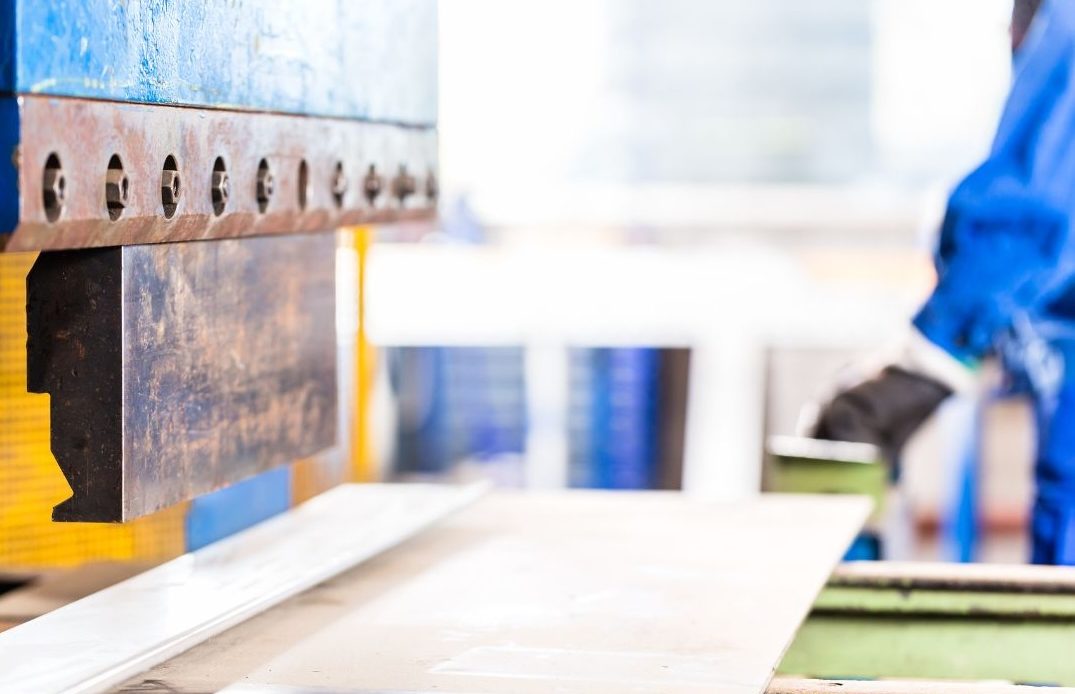
Forming reshapes flat sheet metal into three-dimensional structures, preparing components for their intended applications. This process is required for manufacturing parts that meet both functional and design requirements, whether for structural purposes, intricate profiles, or decorative elements. It is widely applied across industries such as automotive, aerospace, and construction.
Forming not only shapes the material but also improves its mechanical properties through work hardening, increasing resistance to stress and deformation. With advancements in CNC technology, forming processes now achieve higher precision, allowing manufacturers to produce consistent and reliable results even for complex geometries and high-volume production.
Bending
Metal bending is one of the most common forming techniques. A press brake applies force to fold metal sheets at precise angles, creating components such as brackets, frames, and enclosures. CNC-controlled press brakes deliver outstanding accuracy and repeatability, accommodating intricate geometries and thicker materials with ease.
This technique works effectively with a variety of metals and thicknesses, making it a versatile solution for industries requiring durable yet precise components. Its ability to produce consistent bends ensures manufacturers can meet stringent quality standards across a range of applications, including transportation and construction.
Stamping
This process excels in manufacturing automotive body panels, electronic connectors, and decorative parts that require intricate designs and consistent quality. This uses a die and punch to press metal into predefined shapes, making it ideal for high-volume production.
Stamping can also involve additional steps like embossing, flanging, or coining, adding functional or aesthetic features to the metal. Its efficiency makes it a cost-effective choice for large-scale projects, where high repeatability and uniformity are essential for success. It also accommodates a range of materials, expanding its use across industries.
Roll Forming
Roll forming is a continuous process where sheet metal passes through a series of rollers, gradually shaping it into uniform profiles such as beams, channels, or rails. This method is particularly well-suited for producing long, consistent parts.
Industries like construction and transportation benefit greatly from roll forming due to its scalability and precision. The process ensures consistent results even for high-volume production runs, making it an indispensable choice for structural applications and vehicle components. Its energy efficiency and low material waste make it a sustainable manufacturing option.
Welding
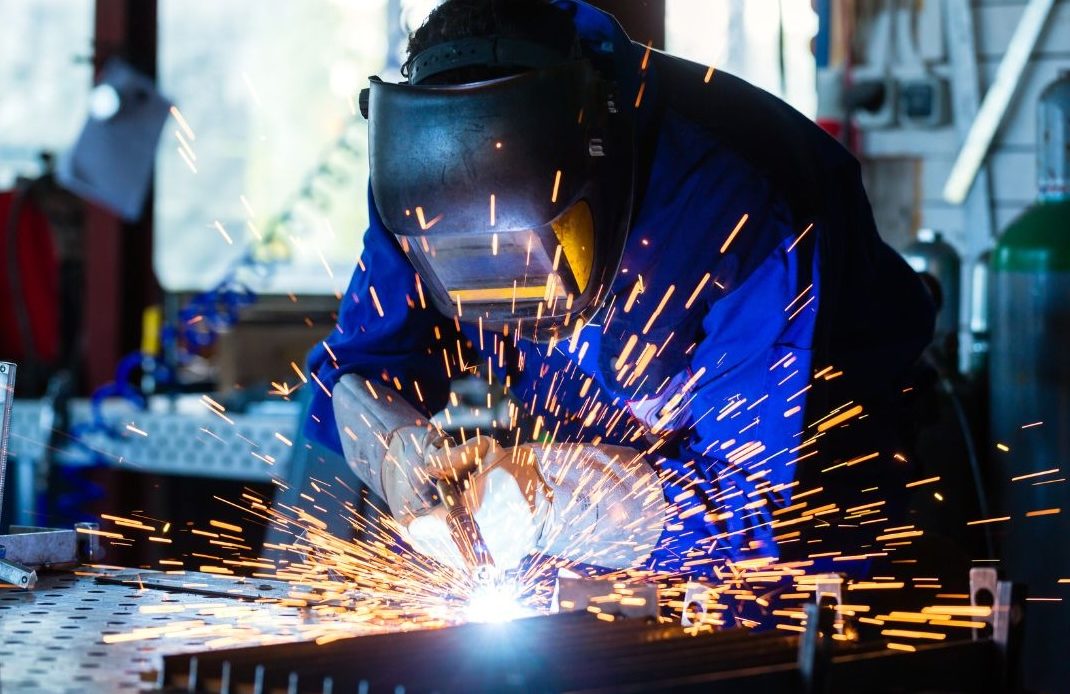
This step is useful for creating secure connections that meet the structural and operational needs of the final product. Various techniques of metal welding including MIG, TIG, and spot welding, are chosen based on material properties and project requirements.
MIG Welding
This is a practical method for welding and joining thicker materials. Its continuous wire feed and shielding gas allow for fast, clean welds, making it ideal for industrial machinery, automotive frames, and structural supports. MIG welding is often preferred in high-volume projects due to its speed and efficiency. The flexibility of this method also accommodates different materials, offering consistent results across diverse applications.
TIG Welding
This type of welding offers unmatched precision, making it well-suited for intricate designs and thin materials. Using a tungsten electrode and shielding gas, it produces clean welds with minimal distortion. Aerospace and medical device manufacturing frequently use this method for its accuracy and professional finish. TIG welding is particularly advantageous in projects requiring superior aesthetics or tight tolerances.
Spot Welding
Spot welding is highly effective for joining overlapping sheets of metal. By applying heat and pressure to specific points, it forms strong connections without additional materials. This technique is widely used in automotive manufacturing to assemble frames and layered components efficiently. It also excels in creating durable joints for parts that undergo significant mechanical stress.
Finishing

This is the final stage of the fabrication process, improving the durability and appearance of components while adding protective features. This stage helps make sure that the final product meets both functional and visual standards.
Painting and Powder Coating
Painting provides a protective layer and custom finish, shielding the metal from corrosion while allowing for a variety of colours and textures. Metal powder coating, a more durable alternative, forms a hard, scratch-resistant surface suited for industrial tools, furniture, and outdoor equipment.
Galvanising
This involves applying a layer of zinc to protect the metal from rust and environmental damage. This technique is essential for structural supports, marine equipment, and fencing exposed to harsh conditions.
Anodising
Anodising is commonly used for aluminium, creating a corrosion-resistant finish and improving the metal’s appearance. This method is frequently used for architectural applications, electronics, and decorative items where durability and aesthetics are equally important.
Polishing and Buffing
This refines the surface of the metal, providing a smooth or reflective finish. These techniques are often used for luxury goods, decorative pieces, and high-end appliances, adding an attractive visual quality to the final product.
Assembly
Assembly integrates individual parts into complete products, ensuring cohesive functionality. Riveting creates durable, flexible connections ideal for modular systems in industries like aerospace and construction. PEM inserts provide secure, flush fastenings within sheet metal, while bonding methods, such as adhesives, enable lightweight, seamless designs—perfect for electronics and decorative applications.
Electrical assembly combines wiring and circuitry into sheet metal housings, providing compatibility and functionality for consumer electronics and industrial equipment. Prototyping transforms CAD designs into physical models, allowing manufacturers to test and refine products before large-scale production. Techniques like 3D printing and CNC machining enable precise prototypes with short lead times, reducing waste and avoiding costly errors.
By incorporating advanced design, prototyping, and assembly processes, manufacturers can produce high-quality components that meet exact specifications. This ensures efficiency and aligns final products with industry standards, forming a strong foundation for any project.
Each stage of this process —design and prototyping, cutting, forming, welding, assembly, and finishing—contributes to creating components that meet the diverse needs of industries such as construction, aerospace, automotive, and electronics.
Advancements in technology, including CNC machinery and innovative finishing sheet metal techniques, have increased the quality and efficiency of fabrication. These improvements enable manufacturers to deliver reliable results while minimising waste and increasing sustainability.
If you’re looking for professional and high-quality sheet metal fabrication services, Greengate Metal Components can bring your ideas to life. Our expertise spans every stage of the process, making sure your project requirements are met with precision and care. Contact our team today to discuss your next project and discover how we can support your manufacturing goals.