Welding might seem like it’s all sparks and steel, but what really makes a structure hold together is the joint. The way two metal parts are fused affects just about everything—how strong the connection is, how it looks, how long it lasts, and whether it can handle a load or not.
In sheet metal welding, selecting the right joint isn’t just about getting the job done—it’s often what decides whether a design succeeds in real-world use. Different shapes, thicknesses, and load demands all play their part in picking the best joint for the job.
So, if you’re at the early design phase, or sketching out a prototype, this quick guide should give you a better handle on which joints make sense for what purpose.
Butt Joint
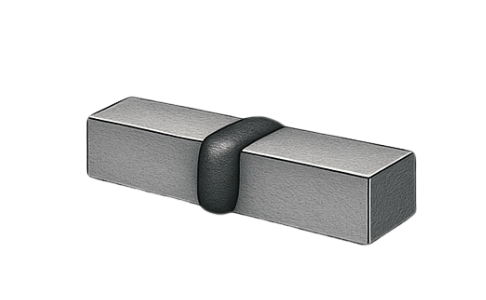
The butt joint is probably the most straightforward type of weld there is. Two metal pieces are placed side by side on the same plane, and the weld runs along the seam where they meet. Simple? Sure. But it’s also widely used because it gets the job done in a clean, no-fuss way.
You’ll find this joint type in everything from flat sheet panels to structural frames, especially where large surface areas need to be joined without overlapping. It tends to work best when the metal edges are perfectly aligned and cleanly prepared.
Common uses:
- Panel fabrication
- Joining pipes or plates in pressure vessels
- Automated welding setups in large production runs
Pros: It’s easy to align, doesn’t waste material, and works well with most welding techniques.
Cons: Not great for high-stress applications unless reinforced or backed. Any gaps or poor prep work can cause weak points.
T-Joint
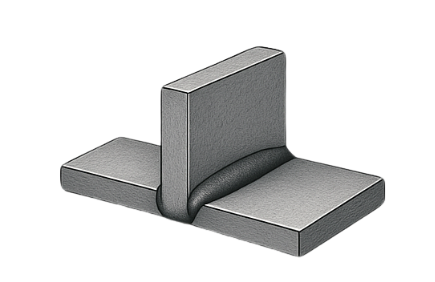
As the name suggests, a T-joint happens when one piece of metal is welded at a right angle to another—forming, well, a T-shape. It’s a go-to joint for building frameworks, supports, and other structures where two parts meet at 90 degrees.
You’ll often spot this in things like machine frames, base plates, and chassis builds. It’s particularly handy in custom assemblies where different parts need to be joined with strong perpendicular welds.
The most typical weld here is a fillet weld—a triangular weld that fills the space between the two pieces. That said, plug welds and slot welds sometimes get used if the pieces are thick or oddly shaped.
Used in:
- Frames and bracing
- Table legs and support beams
- Structural connections in custom builds
Just a little attention to edge prep and proper weld size usually keeps this joint working smoothly—even under load.
Corner Joint
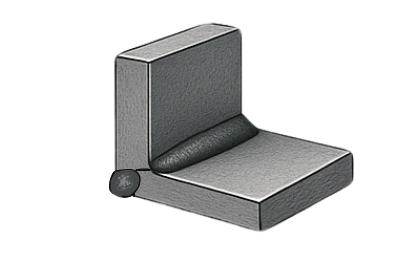
The corner joint is what you’d expect to see when two metal pieces meet at the edge to form an L-shape. It’s used a lot in creating box-style structures—think control panels, metal enclosures, or any frame that needs a clean external edge.
Depending on how visible the joint will be, and how much strength it needs to carry, welders might use fillet welds, bevel-groove welds, or even corner-flange techniques. Each one changes how the joint looks and performs.
Where it shows up:
- Electrical boxes and machine housings
- Lightweight frames for sheet metal builds
- Fabricated corners in furniture or display units
This joint’s biggest advantage is how easily it lets two panels come together at an angle. Just a little care during alignment helps avoid distortion and warping—especially with thinner metal.
Edge Joint
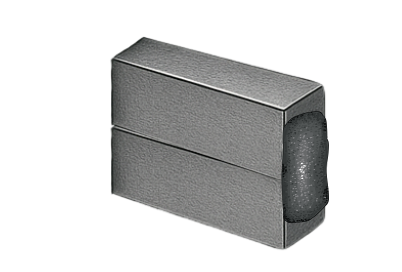
Edge joints are most often used when two pieces of metal sit side by side, touching along the same edge. It’s not about strength—it’s more about creating a seal or connecting thin sheet materials where there’s little to no stress involved.
That’s why you’ll see these joints in tank walls, ductwork, and sheet metal casings. They’re common in designs where appearance matters less than alignment, or where space is tight and overlap would just get in the way.
Ideal scenarios include:
- Ducting systems and ventilation units
- Sheet metal assemblies in HVAC
- Lightweight tanks or containers
Since there’s not much surface area to weld, edge joints usually work best when the pieces are either flanged or backed for extra support. Otherwise, they can be a bit fragile under stress or vibration.
Flange Joint
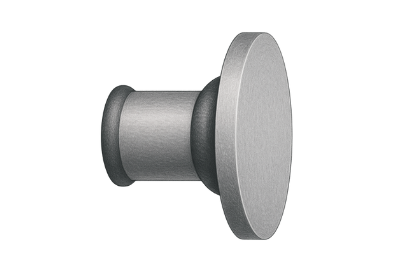
Flange joints aren’t as commonly talked about, but they’re seriously useful in industries where pipes, ducts, or panels need to be joined with both strength and a reliable seal. They work by welding flared or bent edges—usually of circular or flat metal pieces—together to create a tight, secure connection.
You’ll see these joints a lot in HVAC systems, heavy machinery, or anything that moves fluids or gases. Their structure helps resist pressure changes and minimise leaks, which makes them ideal for performance-critical applications.
Typical applications include:
- Ventilation and extraction systems
- Pipework in industrial plants
- Pressure-bound enclosures or tanks
Flange joints are a bit more involved than a standard overlap or butt weld. But when you need a joint that holds firm under repeated stress or constant use, it’s usually worth the extra effort.
Overlap Joint
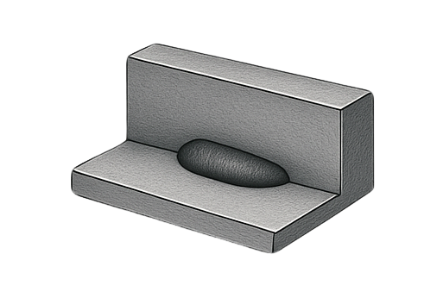
In an overlap joint, one piece of metal sits slightly over the other, and the weld runs along the overlapping edge. It’s simple to put together, especially when working with sheet metal or dissimilar thicknesses where lining up edges evenly isn’t quite possible.
Because of the extra surface area where the metals meet, this joint often offers decent strength without needing a deep weld. It’s often used where neatness is less of a concern and where joints need to be fast, functional, and forgiving.
Industries using this joint:
- Automotive fabrication
- Appliance assembly
- Sheet metal products that don’t need precision finish
Overlap joints work best when corrosion resistance is built in—since the overlapping edge can trap moisture or contaminants if not sealed properly. With the right weld technique, though, they’re tough and efficient.
Pipe Joint
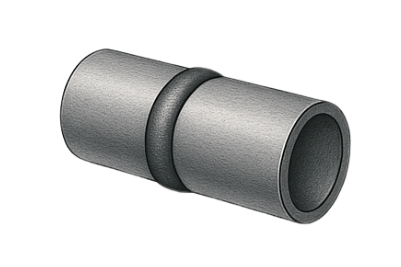
Pipe joints deal with round profiles, which means the approach to welding has to shift slightly. Instead of flat edges or clean corners, you’re working with curved surfaces that need to line up perfectly all the way around—no easy feat if the pipe’s carrying pressure or fluid.
These joints are often used in plumbing, process piping, or structural frameworks involving tubes or cylinders. Welding here needs to account for access, alignment, and strength from all angles.
Common techniques include:
- Orbital welding for clean, automated seams
- TIG welding where precision is key
- Fillet welds for simpler structural joins
Because of the circular shape, even a small misalignment can throw off the whole fit. That’s why pipe joints usually rely on jigs or fixtures to hold everything steady during the weld.
End Joint
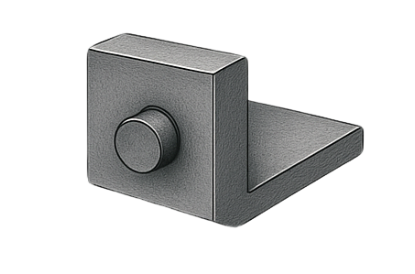
End joints don’t come up as often, but they serve a very specific role—usually where two parts need to meet head-on without overlapping or forming a visible seam. You’ll find them in structures where clean edges matter or in builds that call for a flush, near-invisible connection.
Unlike a butt welding joint, which joins two flat surfaces along the same plane, an end joint often involves welding a cap or plate directly onto the end of a tube or panel. It might be more about sealing off a component than creating structural strength.
Typical uses include:
- Sealing the end of tubes or containers
- Creating smooth terminations in aesthetic builds
- Joining end caps in pressure-retaining systems
The strength comes less from the weld itself and more from how well the fit is prepared. Done right, it’s discreet and reliable.
Getting to grips with the different types of welding joints isn’t just helpful—it’s a smart move if you’re trying to build something that actually lasts. The joint you choose can shape everything from strength to alignment to how the final product performs under stress.
Some joints are all about neat finishes, others are built for pressure or volume. Either way, it pays to know what fits your project before you commit. At Greengate Metal Components, we’ve spent years helping engineers, designers, and manufacturers get the right results—whether it’s a one-off prototype or a full production run. If you’re planning a fabrication job and want clear answers from people who actually know what works, contact us. We’re here to help you build it right.