Selecting the right cutting technology is crucial in sheet metal fabrication. Two of the most commonly used methods, CNC punching machines and CNC laser cutting offer unique advantages tailored to different applications.
CNC punching excels in processing repetitive shapes like holes or slots, while laser cutting is ideal for intricate designs and handling thicker materials. Both technologies are essential tools, but the best choice depends on material compatibility, precision, cutting speed, cost, and edge quality.
In this article, we’ll compare CNC punching machines versus CNC laser cutting, examining their strengths, limitations, and applications. By understanding these differences, you’ll be better equipped to choose the most effective solution for your project, whether it’s high-volume production or precision engineering.
What is a CNC Punching Machine?
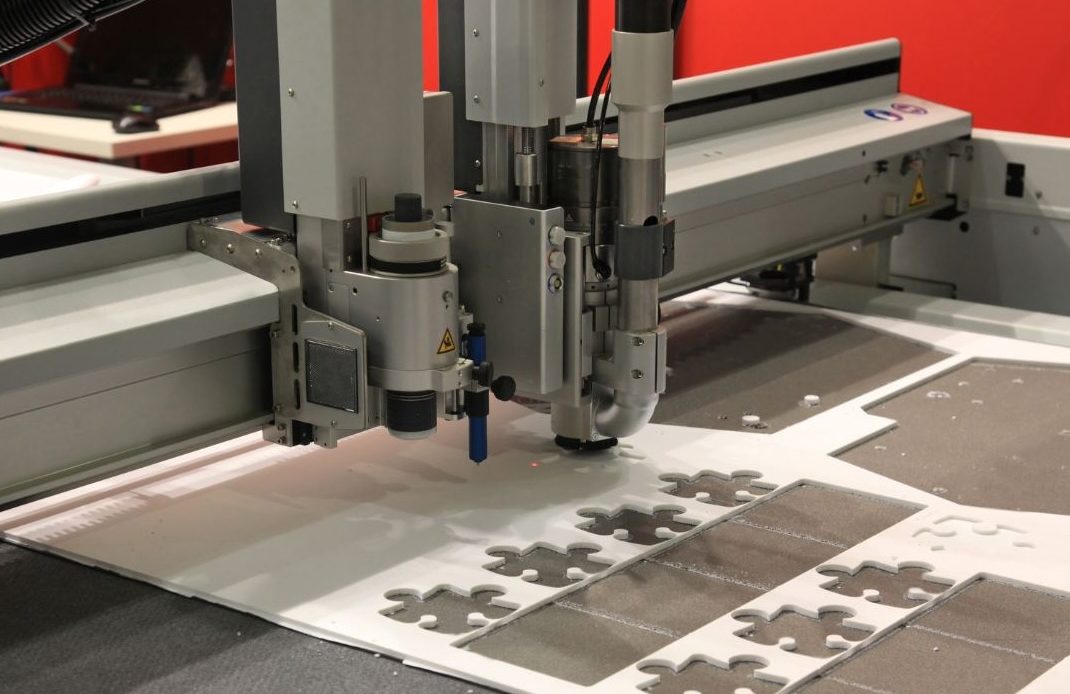
CNC (Computer Numerical Control) punching machines use computer-guided tools to cut, shape, or perforate sheet metal. By pressing a punch tool through the material onto a die, they produce precise holes, slots, or simple cutouts efficiently.
Punching machines are best suited for thinner sheet metals, such as mild steel up to 3mm and aluminium up to 6mm. They excel at repetitive designs with standard shapes like circles and rectangles, making them ideal for perforated panels or parts with densely packed cutouts.
Another key benefit of CNC punching is its heat-free process, which avoids distortion and preserves the flatness of the material. This makes it suitable for automotive components, structural parts, or other applications where heat distortion must be avoided.
However, punching machines are less suited for thick materials or intricate designs, where the availability of tooling limits flexibility.
What is a CNC Laser Cutting Machine?
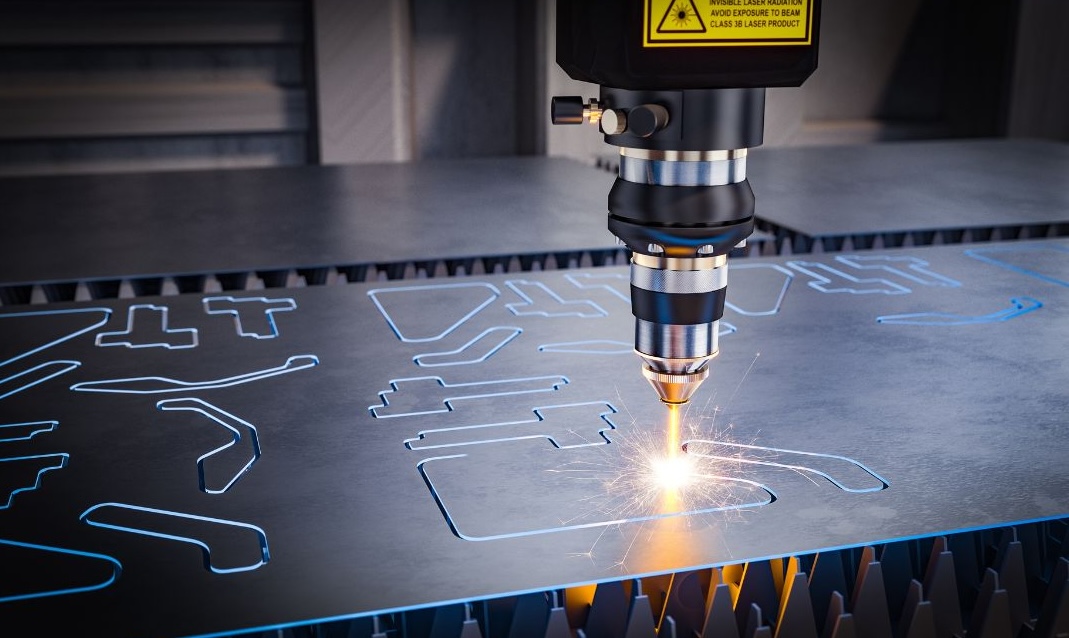
CNC laser cutting machines use a focused laser beam to cut through sheet metal with precision. They create intricate designs and clean edges without physical contact by melting or vaporising the material.
Laser cutting is particularly effective for thicker sheet metals, with fibre lasers at Greengate Metal Components capable of cutting mild steel up to 25mm thick. The non-contact process allows for tight tolerances (±0.1mm to ±0.15mm) and detailed geometries, making it ideal for aerospace, medical, and pharmaceutical components.
Laser cutting also eliminates the need for tooling, reducing setup time and offering flexibility for prototyping, low-volume runs, or parts requiring frequent design changes. This versatility makes it the go-to choice for components with large outside profiles or curved designs.
While laser cutting handles intricate designs efficiently, it is less suited for repetitive shapes whereas CNC punching machines can operate faster with proper tooling.
Material Compatibility
Material compatibility is a key factor when comparing punching machines to laser cutting.
Punching machines are better for thinner sheet metals, such as mild steel (up to 3mm) or aluminium (up to 6mm). They excel at processing repetitive shapes, such as holes and slots, particularly for components like perforated panels or vented covers. Punching is also a heat-free process, ensuring material flatness and structural integrity.
Laser cutting is ideal for thicker materials, such as mild steel (up to 25mm) or stainless steel. Its precision and flexibility make it effective for complex profiles or curved designs that punching machines cannot handle. The smooth edges produced by laser cutting often eliminate the need for secondary finishing, making it a preferred choice for industries requiring high-quality finishes, such as aerospace and medical manufacturing.
For thin metals with numerous small holes, punching machines are faster. Conversely, for intricate designs or thicker materials, laser cutting is the superior option. The choice depends on the material’s thickness, the design’s complexity, and whether heat distortion is a concern.
Precision
Both CNC punching machines and CNC laser cutting machines offer high precision, but they differ in how they achieve it.
Punching machines achieve tolerances of approximately ±0.2mm, making them suitable for standardised designs like vented panels. However, since punching involves physical contact, slight tool marks or burrs may occur, especially on harder metals. These imperfections can be managed with deburring or other finishing processes.
Laser cutting offers greater precision, with tolerances as tight as ±0.1mm to ±0.15mm. The non-contact process ensures smooth, accurate cuts free from tool marks, making it ideal for aerospace, medical, or pharmaceutical components where precision is critical.
While punching is better for high-volume production of repetitive parts, laser cutting excels in intricate designs or projects requiring tight tolerances and clean edges. The choice depends on the complexity and precision requirements of the part.
Cutting Speed
Cutting speed depends on the design, material, and production volume when comparing methods.
Punching machines are faster for repetitive patterns with simple shapes, such as holes or slots. For example, components with densely packed holes can be completed quickly using pre-set tooling. However, punching requires tool setup, which can take up to 30 minutes, making it less efficient for small runs.
Laser cutting is faster for complex profiles or curved designs. With no need for tooling, it offers a significant advantage in prototyping or low-volume production. Our fibre lasers here at Greengate Metal Components can cut at speeds of up to 300 metres per minute, depending on material thickness and design complexity.
For high-volume repetitive parts, punching is more efficient. For low-volume or intricate parts, laser cutting’s speed and flexibility make it the better option.
Cost
Cost considerations play a vital role in choosing between punching machines and laser cutting.
Punching machines require a lower upfront investment but incur ongoing tooling costs, which can add up for custom designs. However, for high-volume production, they are cost-effective due to their speed and efficiency.
Laser-cutting machines have a higher initial cost, especially for industrial-grade fibre lasers. However, they save on setup and tooling costs, as no physical tools are required. Operational expenses may include energy consumption and assist gases like oxygen or nitrogen, which can increase costs for large-scale production.
For high-volume repetitive parts, punching machines are more economical. Laser cutting is more cost-effective for low-volume runs, prototypes, or complex designs, where tooling costs and setup times would make punching inefficient.
Edge Quality
Edge quality is another critical factor when comparing CNC punching machines vs CNC laser cutting.
Punching machines often leave tool marks or burrs on the edges, especially for harder metals. These imperfections usually require deburring or other secondary finishing. Punching is best suited for structural parts where edge appearance is less critical.
Laser cutting produces clean, smooth edges with minimal post-processing needed. This makes it ideal for aerospace, medical, or pharmaceutical components, where edge quality is essential. However, laser cutting can create minor heat-affected zones (HAZ) on thicker materials, though these are rarely problematic for most applications.
For projects prioritising aesthetics or precision, laser cutting is the better choice. For functional components where edges are less important, punching machines are more practical.
CNC punching machines and CNC laser cutting machines each have distinct strengths.
- CNC Punching: Ideal for high-volume, repetitive designs with standard shapes and thinner metals.
- CNC Laser Cutting: Better for complex profiles, clean edges, and thicker materials, with minimal setup time.
The choice depends on your project’s material, precision, volume, and aesthetic requirements. At Greengate Metal Components, we offer both technologies to deliver high-quality results for sheet metal fabrication.
Contact us today to discuss your project, and our team will guide you toward the best cutting solution for your needs.