If you’re developing something complex or bespoke, juggling different suppliers can feel like herding cats. That’s why more firms are switching to comprehensive metal fabrication services—where everything happens in one place, from drawings to delivery. It’s not just easier to manage, it actually makes a huge difference to the finished product too.
When you’ve got one team handling the entire process, things tend to run a lot smoother, faster, and with fewer crossed wires. Over the next few sections, we’ll break down how end-to-end metal fabrication benefits your project, from better timeframes and consistency to cost savings and built-in flexibility. To explore our process at Greengate Metal Components in more detail, take a look at our sheet metal fabrication services.
Streamlined Process and Reduced Lead Time
If there’s one thing most design and engineering teams could do without, it’s delays. Multiple suppliers usually mean multiple timelines—and that’s where things start to slip. With integrated metal fabrication solutions, everything works together from the start. You’re not waiting around for someone else to finish a piece of the puzzle. It’s all handled in sync.
This kind of streamlined metal fabrication process keeps production moving, without the gaps and bottlenecks you often get from fragmented supply chains. Communication improves too, since the same people who helped shape your design are there throughout. They already know the job inside out.
What you get is quicker decision-making, fewer revision headaches, and fewer chances for costly missteps. For time-sensitive projects—or those with tight prototyping loops—it can make all the difference.
With our joined-up approach at Greengate Metal Components, from initial sketches to finished parts; it means your deadlines become more realistic, and much easier to stick to. In short, everything gets done faster—and without compromising on quality.
Consistent Quality Control
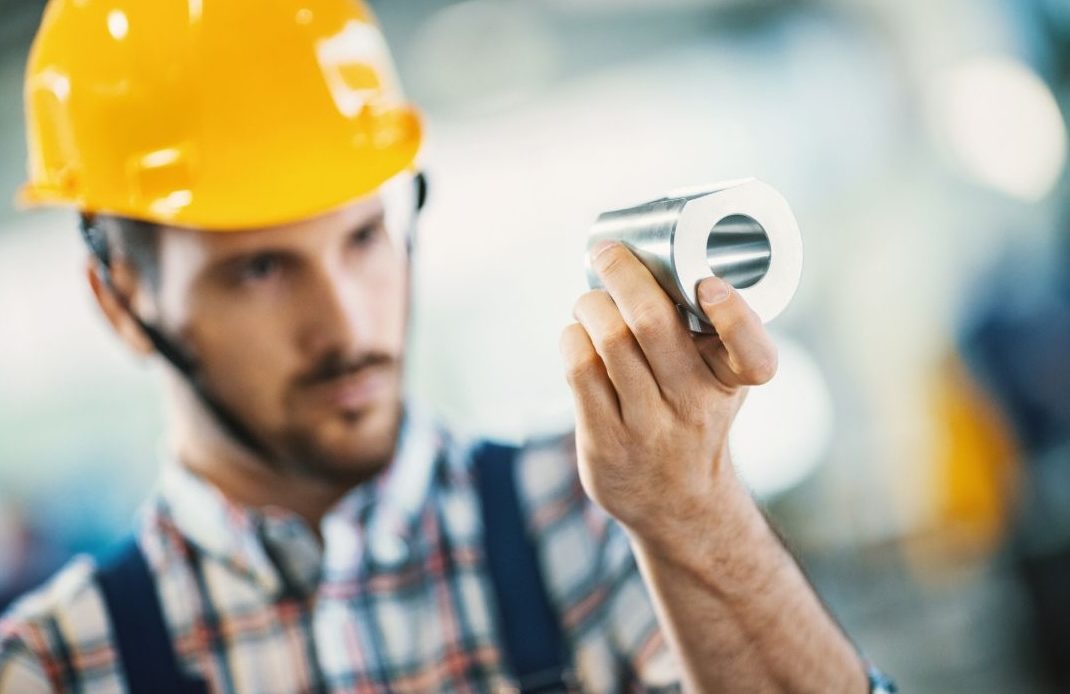
Quality slips often start where handovers happen. If your parts are being passed from one supplier to another, it’s harder to keep standards steady. With comprehensive metal fabrication services, you’ve got one team keeping an eye on things from start to finish—and that, quite frankly, changes everything.
This kind of setup allows for continuous checks throughout the process, not just at the end. For instance, a company might run first-article inspections straight after laser cutting, then again post-welding or finishing. These checkpoints spot issues early, before they become bigger problems later on. It’s not just about preventing mistakes, it’s about locking in consistency.
That level of metal fabrication quality control helps reduce scrap, rework, and surprise costs. Better still, because the same people are handling each stage, there’s a shared understanding of what “good” looks like—no crossed wires, no missed specs.
In a nutshell, if quality matters (and let’s be honest, it always does), working with an end-to-end partner, like ourselves at Greengate Metal Components, gives you far more confidence that what you sign off on is exactly what gets made.
Expertise Across Different Areas of Metal Fabrication
Designs don’t always stay simple. Once things move from CAD to cutting and forming, the job can easily start pulling in five different disciplines at once. That’s where comprehensive metal fabrication services really prove their worth.
Instead of sourcing each step separately, an end-to-end company has every process covered in-house. You’ll usually find experienced teams working across CNC punching, laser cutting, metal folding, welding, and finishing—all on the same shop floor. That means your job can shift from one area to the next without delay or translation errors between providers.
It also helps when your team needs advice or a sanity check on a design. In-house specialists can spot practical tweaks early on that might save you time or material waste later. And because they’re all under one roof, collaboration is faster, simpler, and more useful.
At the end of the day, having all this capability in one place makes a big difference—especially when your project involves tight tolerances, complex geometry, or just the need for everything to actually fit the first time, which we pride ourselves on with our experience and know-how.
Flexibility and Customisation
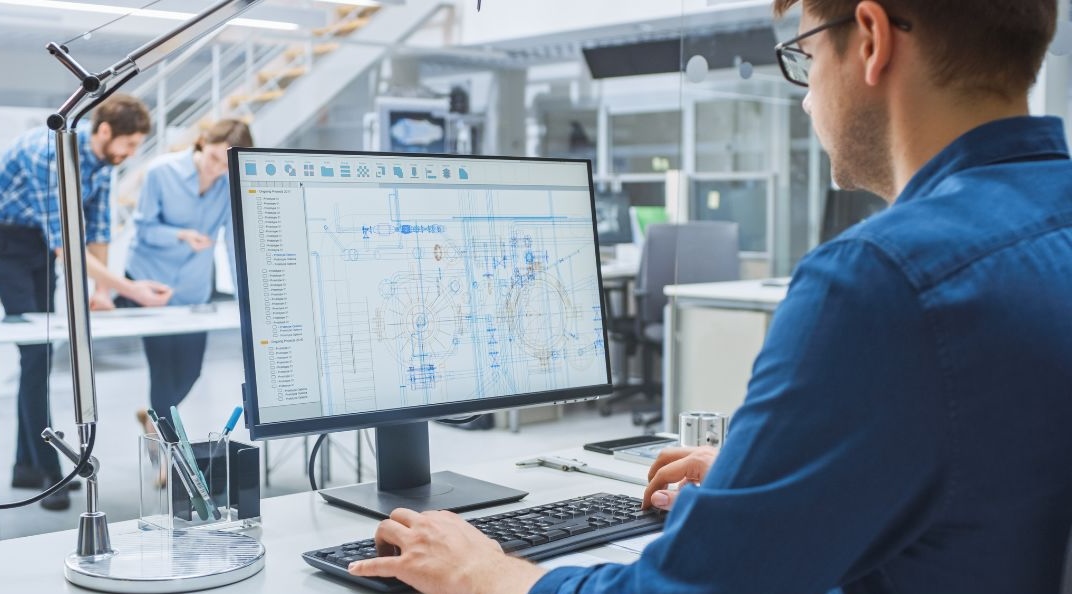
Not every project fits into a neat box, and honestly, that’s where end-to-end providers really come into their own. Because they manage every stage in-house, they’re better placed to offer truly flexible metal fabrication services that shift with your needs—not the other way around.
Need a prototype today, but a short production run next month? No problem. Want to adjust tolerances mid-way through without causing a chain reaction of delays? Still doable. These kinds of custom metal fabrication solutions are far easier to manage when you’re dealing with one integrated team rather than chasing updates from five different shops.
Say, for instance, you need a specific surface finish or have to work around awkward design constraints. A full-service fabricator can usually suggest alternative approaches right on the spot—saving you time and headspace. They know how the different processes affect each other, and that knowledge makes a big difference.
In other words, you’re not just buying parts. You’re tapping into a flexible support system that can adapt fast, without the usual runaround.
Cost Savings
Splitting a project between multiple suppliers might seem cheaper on paper—but the hidden costs stack up quickly. Admin, transport, extra time spent managing communication—it all eats into your bottom line. With comprehensive metal fabrication services, those issues more or less disappear.
One of the biggest metal fabrication cost savings comes from consolidating everything under one roof. You’re not paying for extra freight, duplicated tooling, or time lost to mismatched schedules. There’s less waste, too, because the same team is optimising material use across all stages.
And let’s not forget overheads. Fewer purchase orders, fewer quality checks at hand-off points, and less back-and-forth to clarify specs all translate into time saved—which, more often than not, means money saved too.
For businesses under pressure to deliver on tighter budgets or timelines, those benefits aren’t just nice-to-haves. They’re a big part of staying competitive.
So while the hourly rate might be the same (or even slightly higher), the total cost over the project’s lifespan usually tells a very different story.
Choosing a supplier isn’t just about price—it’s about trust, timing, and getting the job done right the first time. With end-to-end metal fabrication benefits, with Greengate Metal Components, you gain more than just components; you get a smoother process, greater control, and better long-term value.If your projects demand precision, flexibility, and consistency, then why not partner with us as a single-source fabricator; it could be the smartest move you make. To discuss your next project, contact us today at Greengate Metal Components.