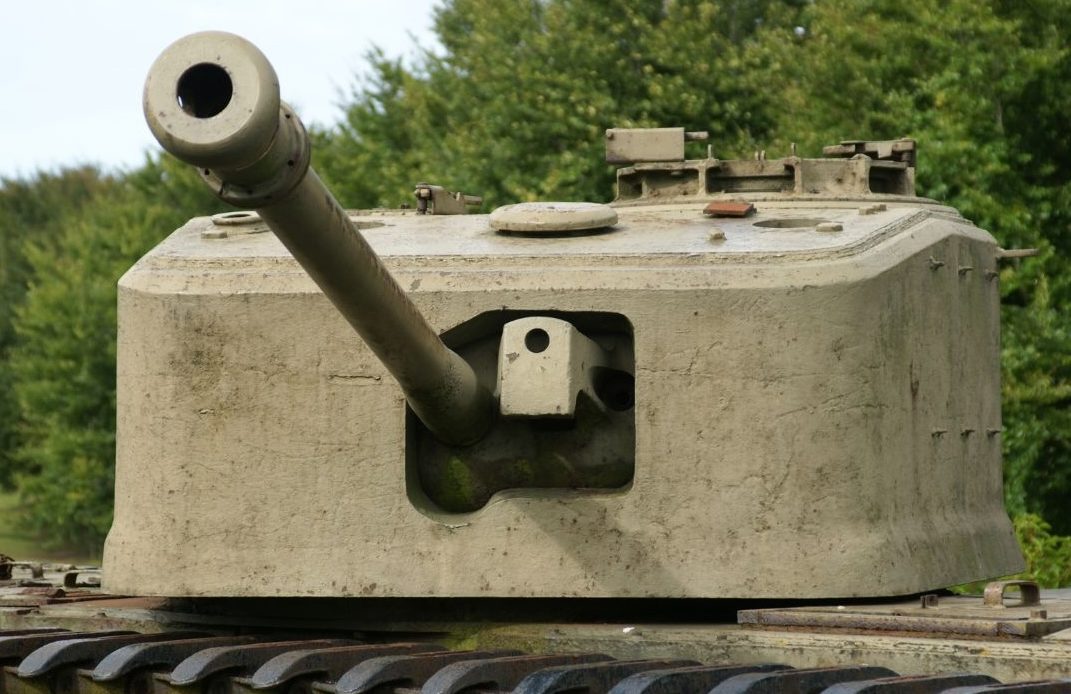
Benefits of Outsourcing Defence Component Fabricating
- Cost savings
- Access to expertise
- Scalability and flexibility
- Faster time-to-market
- Focus on core business activities
Defence Industry Components We Can Manufacture
- Armoured protection
- Radar components
- Heat shield components
- Electronic Housings
- Operational land, marine and aerospace equipment
- Components and subassemblies for military vehicles
- HVAC components
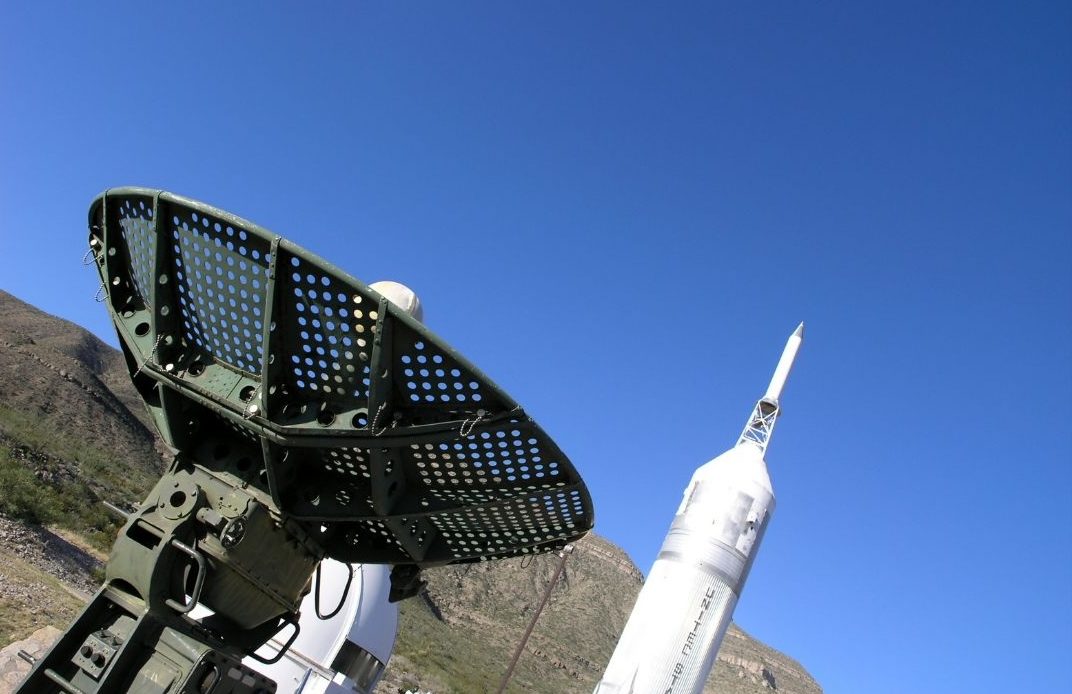
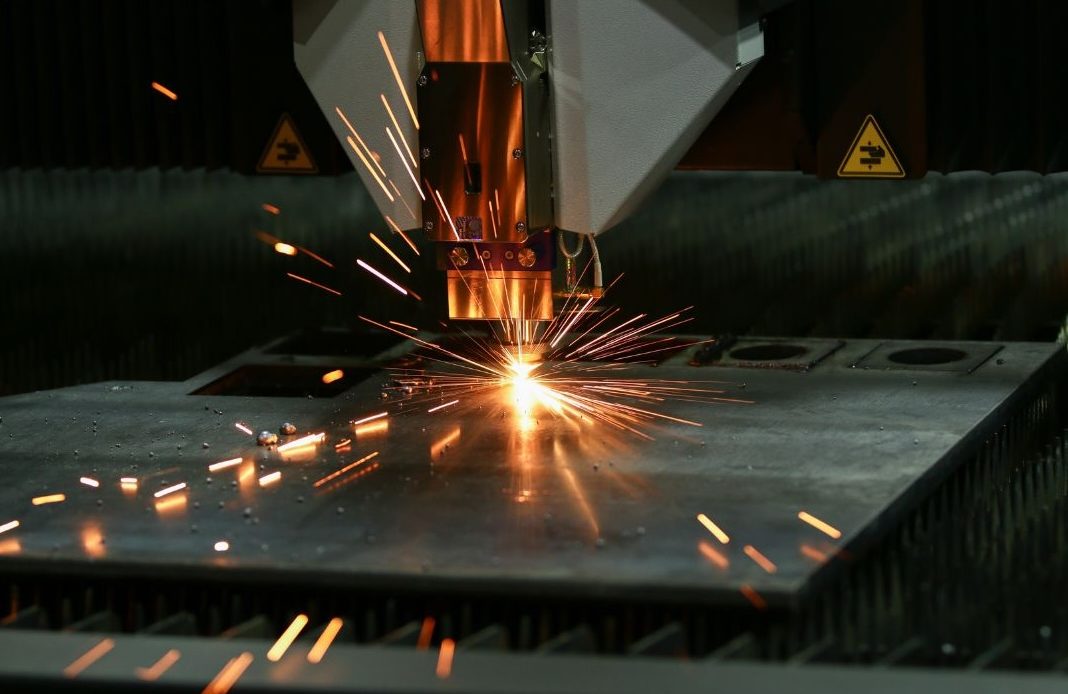
Tailored Metal Solutions for the Defence Industry
At Greengate Metal Components, we use advanced CNC laser cutting machinery to deliver precise and efficient metal component fabrication.
Our laser-cutting technology ensures each piece is cut with accuracy, allowing us to produce detailed shapes and designs from a variety of materials. Whether it’s steel, aluminium, or stainless steel, our CNC machines provide incredible precision, ensuring top-quality results for your military components.
Interested in Sheet Metal Fabrication for the Defence Industry?
Contact us today to discuss your requirements and find out how we can help.
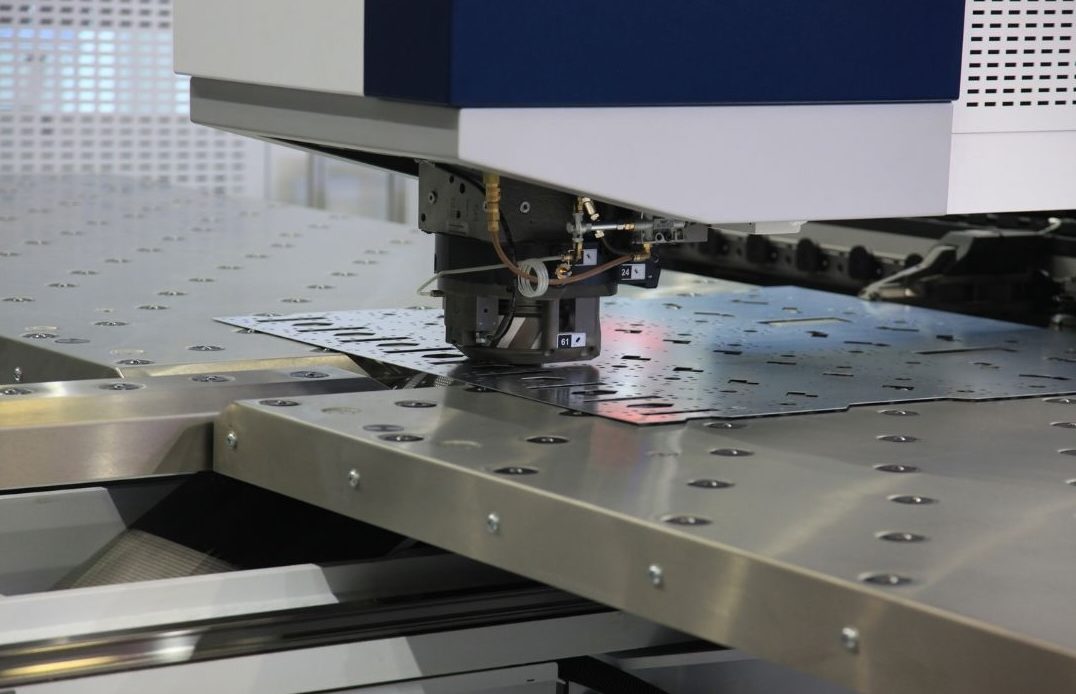
We Have The Experience and Knowledge To Help
At Greengate Metal Components, we bring over 75 years of experience in sheet metal fabrication to support the defence industry in producing high-quality, durable components.
We understand the unique challenges of creating reliable, robust parts for demanding defence applications. Our team works closely with you during the design and engineering phases, offering valuable insights to optimise component performance, reduce production costs, and improve manufacturability, ensuring your military systems are built to the highest standards.
Our Machinery
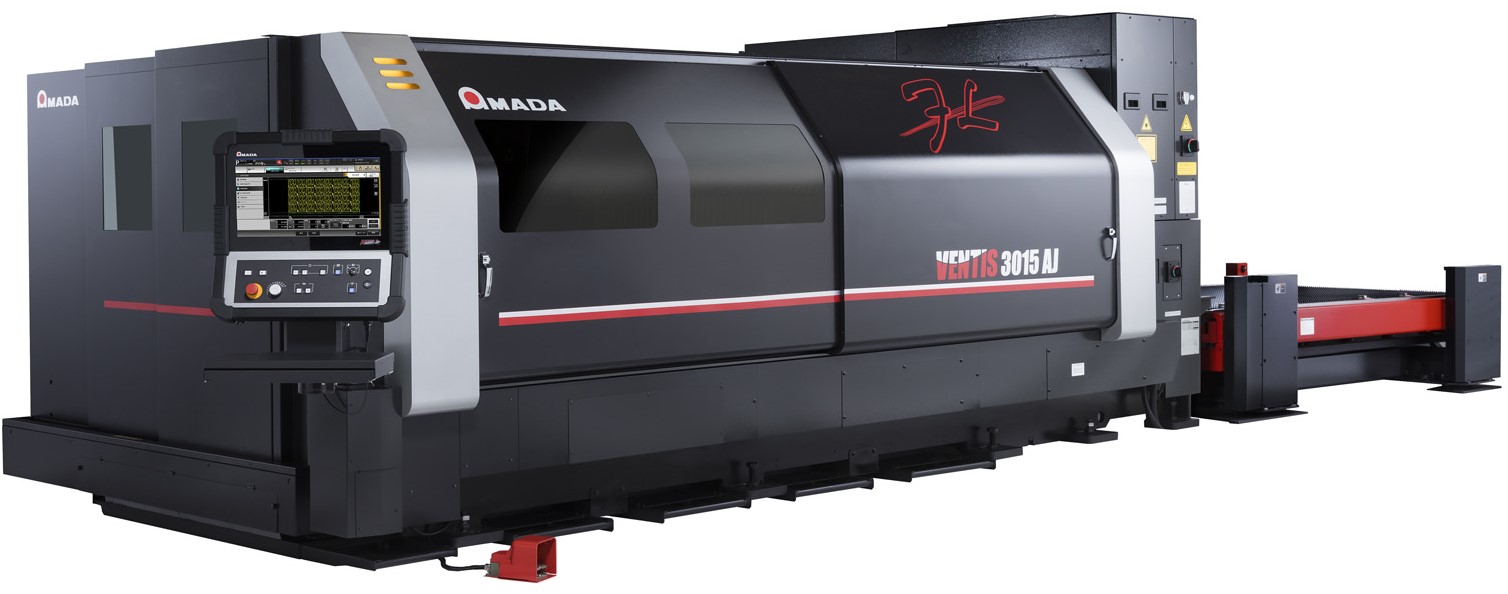
CNC Laser Cutting Machine
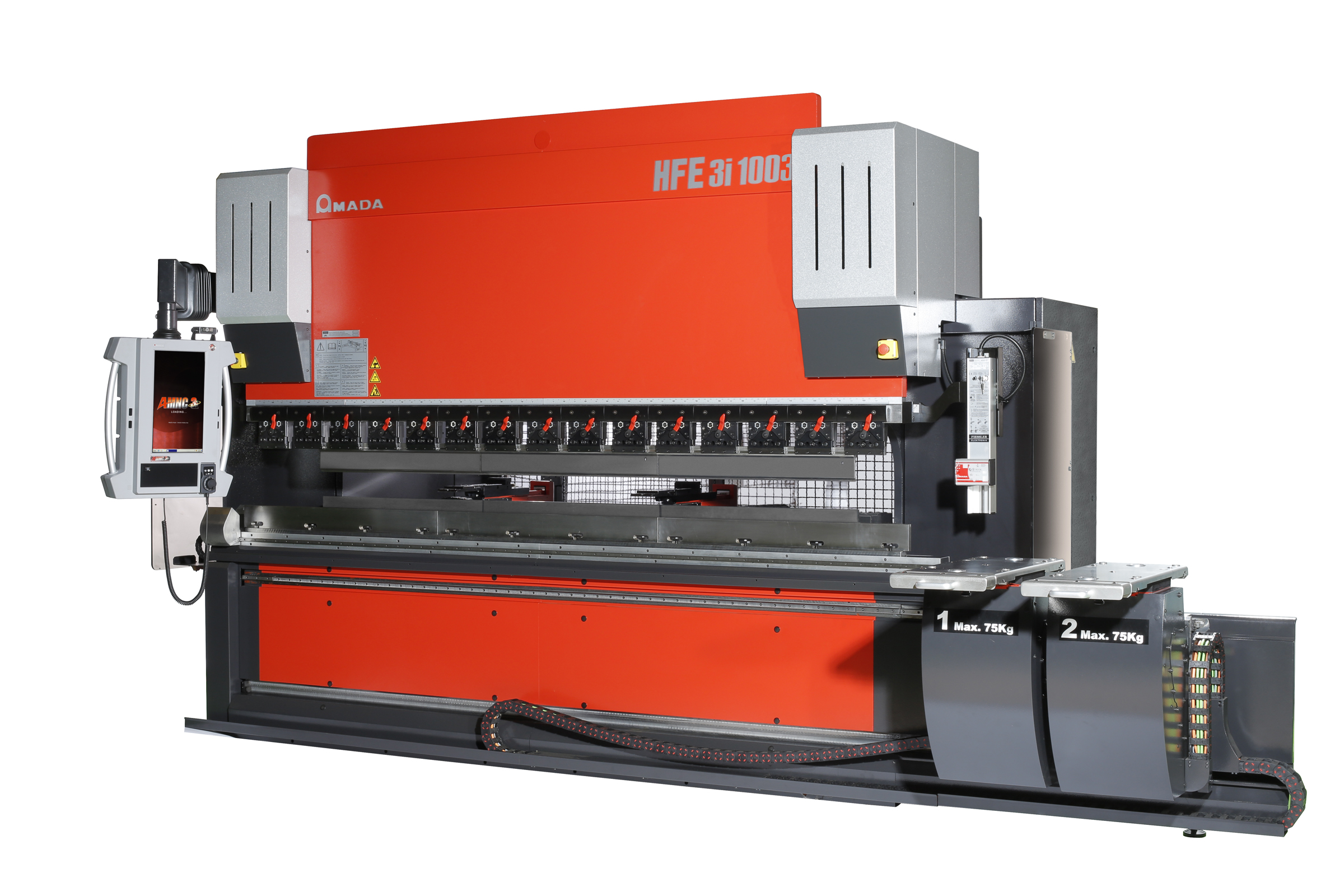
AMADA HFE3i
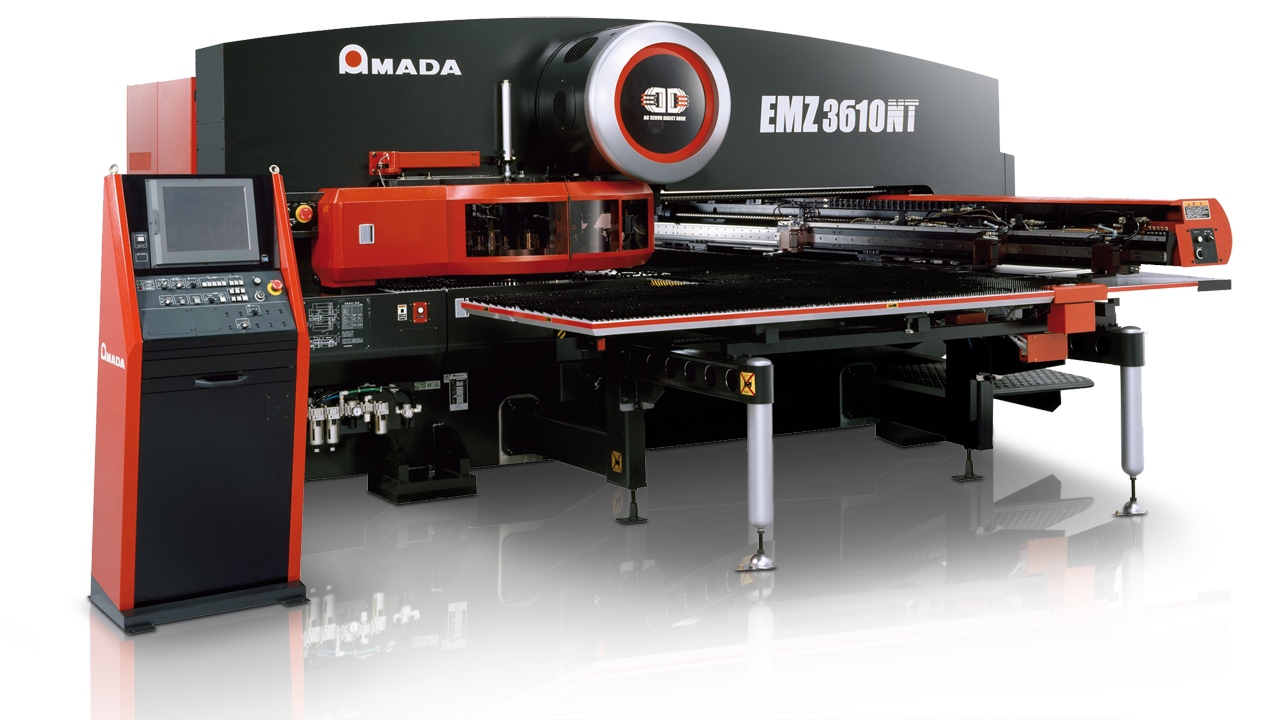
AMADA EMX-3610
The optional tool identification systems and dedicated tapping units reduce setup times and allow for even more process integration for higher efficiency.
Frequently Asked Questions
Defence industry sheet metal fabrication is the process of manufacturing precise and durable metal components for use in defence equipment and systems. This includes items such as vehicle armour, radar system enclosures, aircraft panels, and naval components. The fabrication process involves cutting, bending, welding, and assembling metal sheets, often using advanced technologies like CNC machines and laser cutting to achieve high accuracy. Components are designed to meet strict standards for strength, reliability, and performance in demanding environments.
Materials commonly used in defence sheet metal fabrication include steel, aluminium, titanium, and stainless steel. Each material is selected based on its properties, such as strength, corrosion resistance, weight, and durability. For example, titanium is often chosen for its strength-to-weight ratio in aerospace applications, while steel is preferred for armoured vehicles. The choice of material depends on the specific requirements of the defence application and the operating conditions.
Precision is critical in defence sheet metal fabrication because the components must meet exact specifications and perform reliably under extreme conditions. Even minor errors can lead to equipment malfunctions, compromising safety and effectiveness. Defence systems often consist of interdependent parts that must fit together seamlessly. Using advanced technologies like CNC machining ensures high accuracy, reducing the risk of failure and enhancing the overall reliability of defence equipment.
The time required to fabricate defence sheet metal components varies based on the complexity and scale of the project. Standard parts may take a few weeks to produce, while intricate designs or large-volume orders may take longer. Factors affecting timelines include material selection, the techniques used, and compliance with strict industry standards. Working with experienced manufacturers can help streamline production while maintaining the required levels of quality and precision.
Quality control is essential in defence sheet metal fabrication to ensure every component meets the necessary standards. Manufacturers typically carry out inspections at various stages, including material testing, dimensional accuracy checks, and stress testing, to confirm durability and reliability. Advanced tools like laser measurement systems and non-destructive testing techniques are also used to identify defects or inconsistencies. These measures ensure that components can withstand the demanding environments where defence equipment operates.
Yes, defence industry sheet metal fabrication can accommodate custom designs. Engineers and manufacturers often collaborate to develop components that meet specific requirements, whether for unique shapes, sizes, or performance needs. Customisation is crucial in the defence sector, where applications often demand bespoke solutions. With tools like computer-aided design (CAD) software and CNC machines, manufacturers can produce detailed, tailored components that integrate perfectly into complex defence systems.
Outsourcing defence sheet metal fabrication provides access to expert knowledge, advanced equipment, and efficient production processes. Experienced manufacturers understand the unique demands of the defence industry and can deliver high-quality components while adhering to strict standards. Outsourcing also helps businesses reduce overhead costs, such as those associated with maintaining in-house production facilities and allows for flexibility in scaling production to meet fluctuating demand.
Defence sheet metal components are designed to endure harsh conditions, such as extreme temperatures, corrosion, and physical impacts. Materials like stainless steel and titanium are selected for their durability, while protective coatings, such as galvanising or anodising, enhance resistance to wear and rust. Rigorous testing during the fabrication process ensures components are fit for use in challenging environments, from desert operations to marine or aerospace applications.
Defence sheet metal fabrication can lower production costs by using efficient methods and technologies that reduce waste and improve productivity. Automation through CNC machines and robotic welding ensures accuracy, which reduces errors and material usage. Experienced manufacturers can also refine designs to maximise material use without compromising strength or performance. Outsourcing fabrication further reduces costs by eliminating the need for businesses to invest in their own facilities, equipment, or skilled labour, while still delivering reliable, high-quality components.