Welding runs aren’t just technical jargon—they’re the building blocks that hold entire structures together. Whether you’re working on a new product design or overseeing sheet metal fabrication or CNC laser cutting services, knowing your way around the types of welding joints can make conversations smoother and decisions sharper.
From a fillet weld on a basic bracket to complex butt weld types for thicker steel, each welding run brings its own purpose. Understanding the differences—say, single vs double welds—could be the detail that shapes project success.
This guide explains 9 core structural welding techniques that show up again and again in real-world fabrication. It’s a straightforward look at common welding joint applications and clears up those head-scratching welding terms, explained with examples that just make sense.
Fillet
A fillet weld tends to be the most common welding run out there, and for good reason. It’s the go-to when joining two metal pieces at a right angle, like in T-joints or lap joints, which pop up everywhere from machinery frames to structural supports. This weld fills the corner between the metals without the need for edge prep, making it quick and cost-effective. But it’s not all smooth sailing. Getting penetration right can be a bit tricky, and poor technique could weaken the joint. Even so, it’s central to everyday welding joint applications in manufacturing.
Square Butt
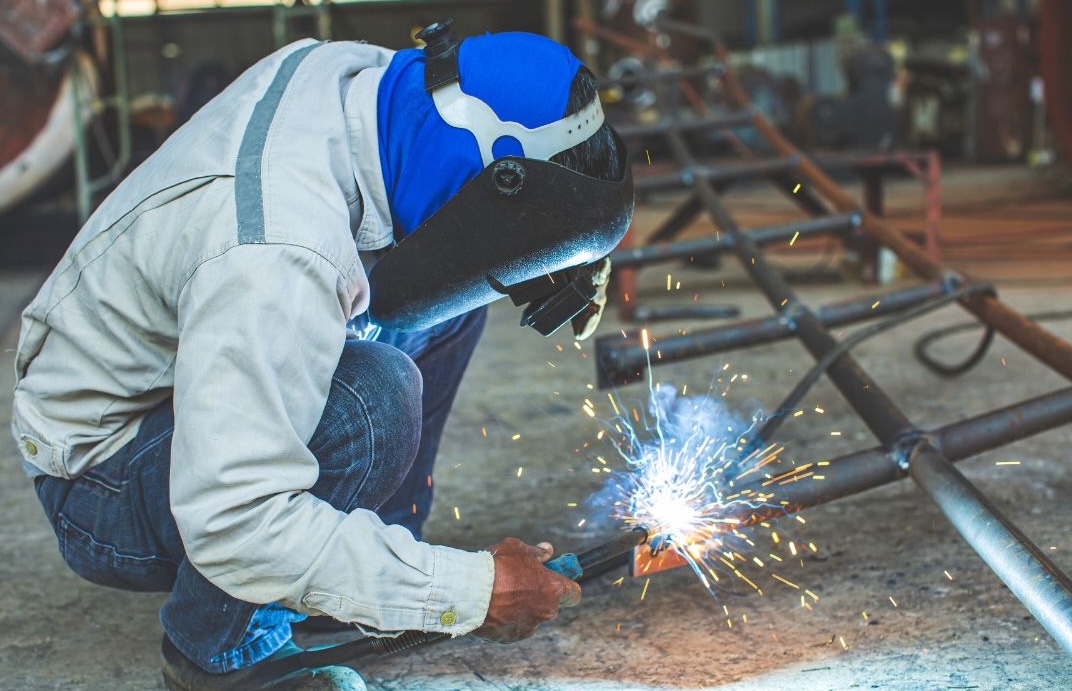
The square butt weld is about as straightforward as it gets—a flat-on-flat welding run where two edges meet in a line. It’s typically used on thin materials, where the need for groove prep is minimal. That simplicity makes it a popular choice in automated welding or when speed matters. But as material thickness increases, it can start to fall short on penetration strength. Among the butt weld types, this one is budget-friendly, though not always ideal for load-bearing joints. Still, it has its place in lighter welding joint applications, especially when accuracy and repeatability are key.
Single V Butt
The single V butt weld steps things up with a V-shaped groove that allows for deeper fusion between metal edges. This type of welding run is often used when material thickness makes a square butt impractical—typically beyond 5mm. The angled cut improves penetration and distributes heat more evenly, which helps avoid weak spots. It’s common in pressure vessels, pipelines, and frames where strength can’t be compromised. Compared to simpler butt weld types, the V shape does call for more prep and filler metal, but the payoff is a solid, consistent join that handles structural demands well.
Double V Butt
A double V butt weld is the upgrade you reach for when thicker materials call for added strength without going overboard on filler. With a V groove on both sides, this welding run balances heat input and helps reduce distortion—something that can be a real headache with heavy plate. It’s often used in structural steelwork or pressure systems where durability matters. Unlike single-sided joints, this type spreads stress more evenly, improving integrity under load. Among butt weld types, it offers one of the better trade-offs between material use and strength, especially when you’re weighing up single vs double welds.
Single U Butt
With a curved groove instead of sharp angles, the single U butt weld stands out for its efficiency on thicker metals. This welding run uses less filler than a V joint and provides smooth, consistent fusion—ideal when neatness and strength go hand-in-hand. You’ll often find it in pressure vessels and structural components where deep penetration is essential. Among welding joint applications, it’s a bit more niche because it needs specialised prep, but when done right, it combines strength with material savings far better than some other butt weld types.
Double U Butt
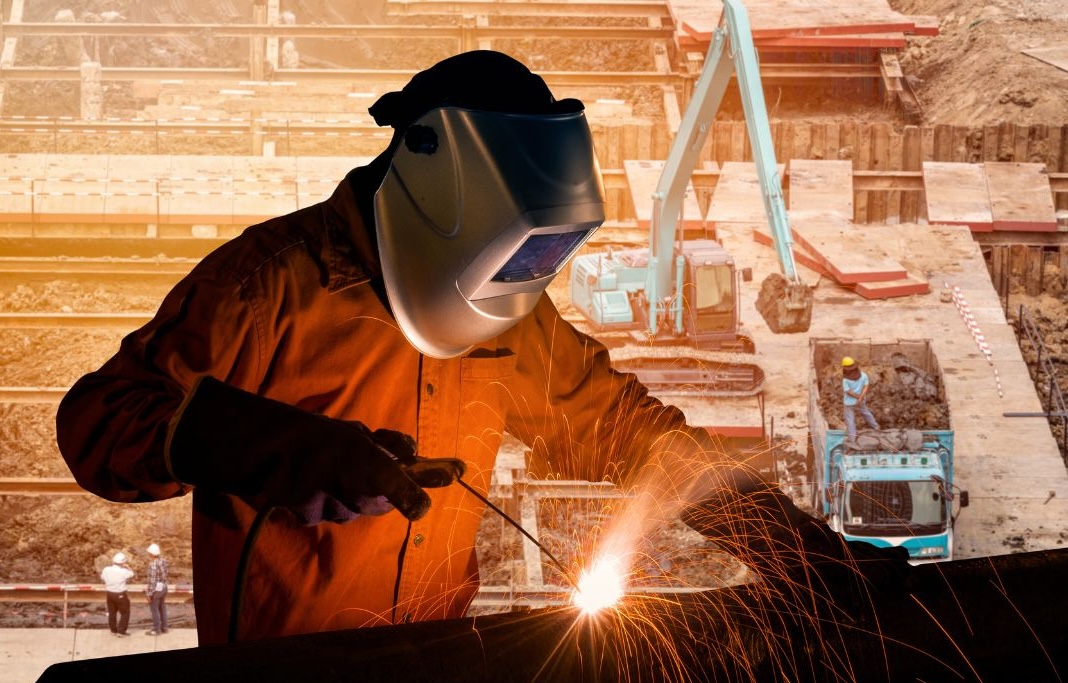
The double U butt weld takes things further, offering solid strength and reduced filler use for thick materials under heavy stress. It’s a go-to welding run for critical structures—think bridges, ships, or high-pressure systems—where every joint needs to pull its weight. With U grooves on both sides, it keeps heat and stress balanced, reducing warping. Of course, it’s not the quickest option. The prep work’s more involved, often needing machining. Still, compared to other butt weld types, it gives better consistency and durability in high-stakes welding joint applications.
Single Bevel Butt
The single bevel butt weld is often the practical choice when you can only access one side of a joint. You’ll see this welding run a lot in pipework and structural assemblies where space is tight or backside welding just isn’t an option. The angled edge helps with fusion, though it usually needs more filler than a V or U groove. It might not be top of the list for every job, but for asymmetrical designs or limited access builds, it’s one of the more versatile butt weld types around.
Double Bevel Butt
Where strength and symmetry matter, the double bevel butt weld is often the answer. With both edges prepped at an angle, this welding run allows for strong, balanced joints, especially in thicker materials that face mechanical stress. It’s common in heavy-duty frames, structural beams, and large-scale assemblies where weld quality can’t be left to chance. Compared with other butt weld types, it tends to need less filler than a V groove, though it still demands time and prep. In welding joint applications, it’s trusted for durability and a cleaner finish.
Single J Butt
The single J butt weld doesn’t show up as often, but it’s handy in specific situations—especially when one side is harder to reach or when working with thick materials. The J-shaped groove allows for smoother metal flow and better control over penetration, which can make the whole welding run more efficient. It’s sometimes preferred in high-strength designs or pressure systems, though the prep can be more complex. Among lesser-known butt weld types, it offers a good mix of strength and filler savings in the right welding joint applications.