What if you could save costs, improve quality, and accelerate your projects—all without major upfront investments? Outsourcing sheet metal fabrication makes this possible. Across industries like construction, automotive, aerospace, and manufacturing, outsourcing is changing how businesses approach metal fabrication.
For industries that demand precision and consistency, outsourcing provides a strategic edge. This article highlights the top five benefits of outsourcing sheet metal fabrication. Whether you aim to cut costs, simplify processes, or improve product quality, outsourcing could be the solution to your business.
1. Cost Savings
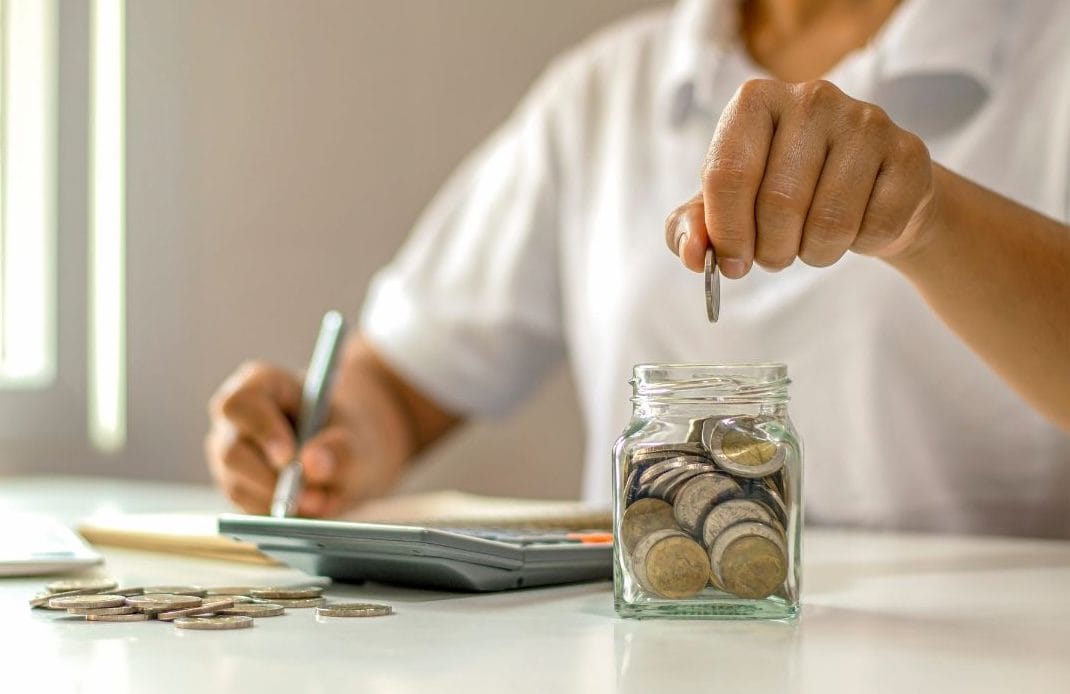
One of the most immediate advantages of sheet metal outsourcing is the cost-effective fabrication that it offers. It enables businesses to access professional-grade facilities without heavy upfront investments. Manufacturing firms could reduce operational costs by up to 25% by outsourcing their sheet metal needs, reallocating savings into research and development.
In addition to equipment costs, outsourcing reduces expenses related to maintenance, training, and operational overheads. Fabrication companies already have skilled workers, advanced tools, and processes in place, meaning your business doesn’t have to spend time or resources on training staff or maintaining equipment.
By working with professional fabricators, businesses also benefit from economies of scale. These companies often handle large orders for multiple clients, reducing per-unit costs for materials and production. As a result, businesses can produce high-quality components at a lower overall expense.
2. Access to Advanced Technology
Outsourcing sheet metal fabrication provides businesses with access to advanced tools and equipment that might be out of reach for in-house operations. Professional fabricators invest in cutting-edge machinery, such as CNC laser cutting, press brakes, and automated welding systems, delivering precision and efficiency in every project.
These technologies improve the accuracy of fabrication and produce consistent results, even for complex designs. For businesses, this means reliable outcomes that meet stringent quality standards. For instance, advanced fabrication technology methods, such as laser cutting, produce components with smoother edges and minimal waste, improving both the aesthetic and functional aspects of the final product. Many businesses have found that by outsourcing, they gain a competitive edge through high-performance materials and precise engineering.
By collaborating with experienced fabricators, companies can meet project demands with confidence, supported by the latest technology and expertise in the industry.
3. Improved Quality
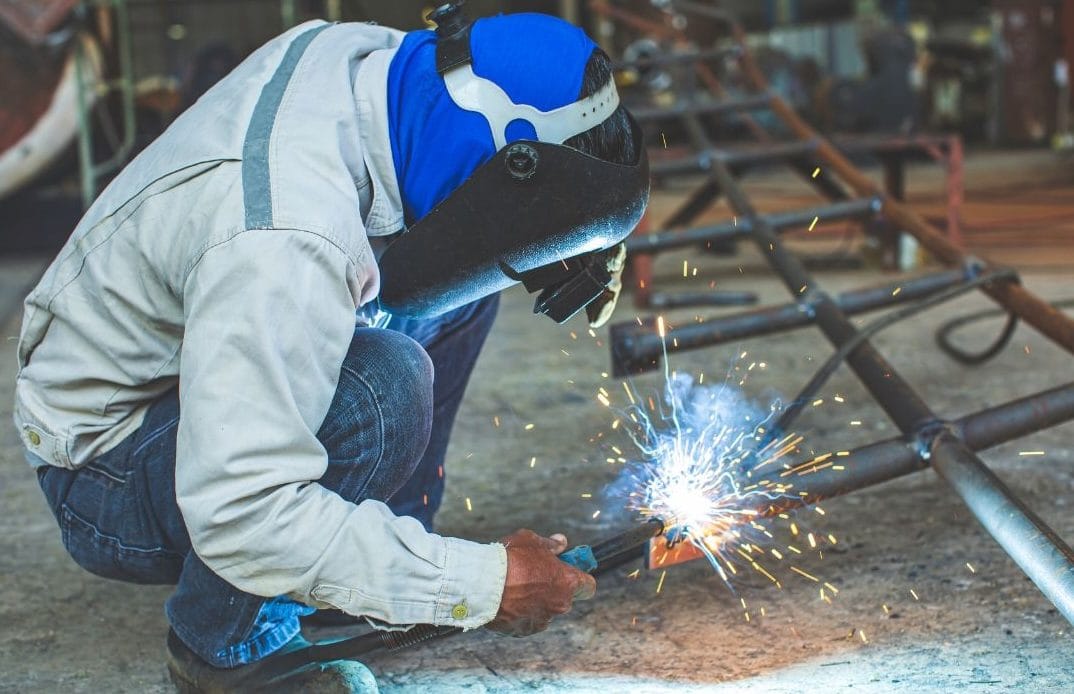
Outsourcing sheet metal fabrication allows businesses to benefit from the expertise and skill of professional fabricators. These companies employ specialists trained to ensure each component meets high-quality and durability standards. This results in fewer defects and a higher level of reliability in the finished products. For businesses, this translates to a reduced risk of product failures and a stronger reputation with customers.
Industries such as aerospace and automotive, where precision and performance are essential, rely heavily on outsourced fabrication to achieve consistently high standards. For example, aerospace manufacturers have found that partnering with experienced fabricators reduces inconsistencies in components, helping to maintain safety and performance benchmarks.
By working with specialists, businesses can deliver products that meet or exceed customer expectations, while avoiding the risks associated with in-house errors or resource limitations.
4. Faster Project Turnaround
Many industries, such as construction and manufacturing, depend on tight schedules where delays can lead to financial losses. Outsourcing sheet metal fabrication helps businesses complete projects more quickly by simplifying production timelines. Professional fabricators have the resources, expertise, and processes in place to handle projects efficiently, even under tight deadlines.
With established workflows and specialised teams, these companies are equipped to manage multiple projects simultaneously. This capability allows businesses to avoid delays often associated with in-house operations. Outsourcing also allows for greater flexibility when changes or adjustments are needed during production. For example, if a manufacturing company faced an urgent production deadline but lacked the resources to complete the task in-house. By outsourcing, they met their delivery date and avoided costly penalties, all while maintaining product quality.
By partnering with professional fabricators, businesses can meet a sheet metal project turnaround with confidence and maintain momentum in their operations.
5. Reduced Labour Requirements
Outsourcing sheet metal fabrication significantly lowers the need for in-house skilled labour. Businesses no longer have to allocate resources to recruit, train, and retain specialised workers for fabrication tasks. This not only helps simplify operations but also shortens product development cycles, resulting in faster market launches.
By reducing the demand for in-house labour, companies can redirect resources to operations such as product innovation and customer service.
Professional fabricators come with pre-established expertise, meaning businesses can avoid the challenges of building an in-house team. This also eliminates the ongoing costs associated with employee benefits, training programs, and managing staff turnover.
By outsourcing, companies can also free up their internal teams to concentrate on core business functions such as product development and innovation, customer service, or sales. This all results in the potential for faster product development cycles and improved market positioning.
6. Manufacturing Solutions and Design Collaboration
Outsourcing sheet metal fabrication supports collaboration between businesses and skilled fabricators, enabling better designs, improved material efficiency, and effective solutions for engineering challenges. This approach helps create components that balance functionality, aesthetics, and cost-efficiency.
Fabricators often recommend design adjustments that reduce waste, enhance durability, or simplify assembly processes. These insights are particularly valuable in industries like aerospace and automotive, where precision and innovation are priorities.
Outsourcing also provides access to experienced professionals who bring advanced manufacturing knowledge. Their input helps businesses achieve practical and scalable designs that meet production demands while maintaining high standards. This partnership allows for quicker project development and smoother production processes, whether for prototyping or large-scale manufacturing.
By working closely with fabricators, businesses can refine their designs, save resources, and improve outcomes, making outsourcing an essential strategy for achieving manufacturing goals efficiently.
Outsourcing sheet metal fabrication can change how businesses operate, delivering measurable benefits across cost savings, quality, speed, and resource management. By partnering with experienced fabricators, like ourselves at Greengate Metal Components, companies gain access to advanced technologies, skilled expertise, and streamlined processes that are difficult to replicate in-house.
Whether your priority is reducing overheads, enhancing product standards, or meeting tight deadlines, outsourcing offers a practical solution to stay competitive. Take a closer look at your fabrication needs and explore metal fabrication partnerships that can help you achieve better outcomes with fewer constraints.