Choosing the right cutting method for metalwork can greatly impact quality, cost, and efficiency. Laser cutting and plasma cutting are two widely used techniques, each with its strengths for various applications. For metalworkers, engineers, and manufacturers, understanding the specific benefits of each method is essential.
This article compares plasma cutting vs laser cutting, and focuses on precision, speed, cost, and practical applications, helping you decide which approach suits your metalworking requirements.
What is Laser Cutting?
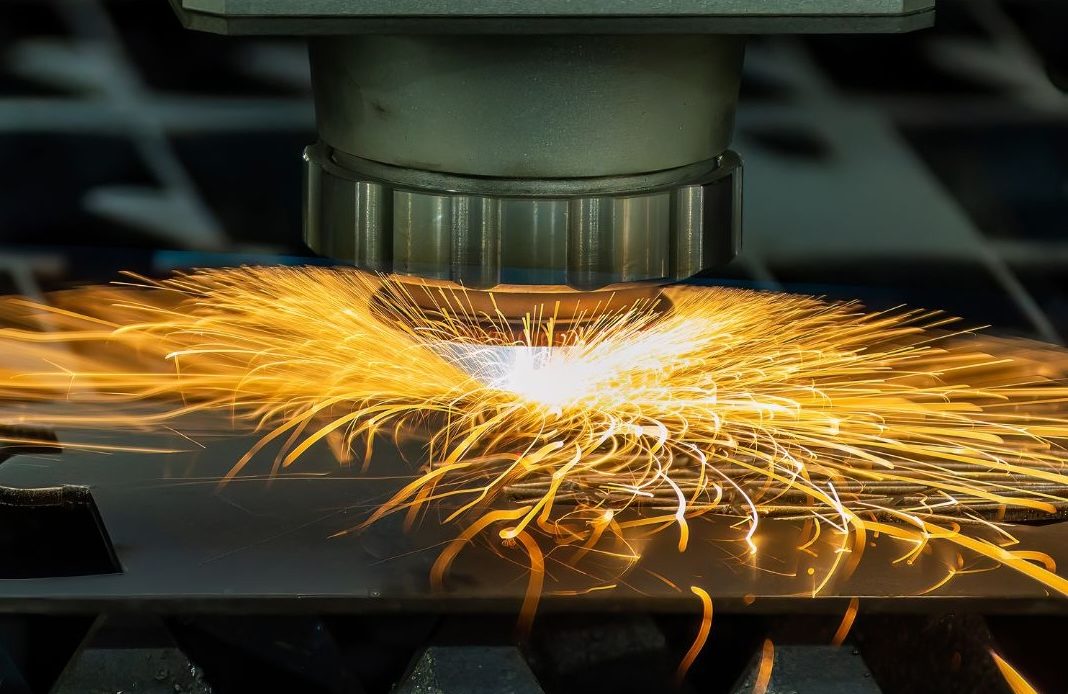
Laser cutting is a method that uses a focused beam of light to cut through metal. This technology was developed in the 1960s and has become a preferred choice for high-precision metalwork. A laser cutting machine typically includes components like a laser source, mirrors, and lenses to direct and concentrate the light. This focused laser beam heats and melts the metal, allowing for clean and precise cuts.
What is Plasma Cutting?
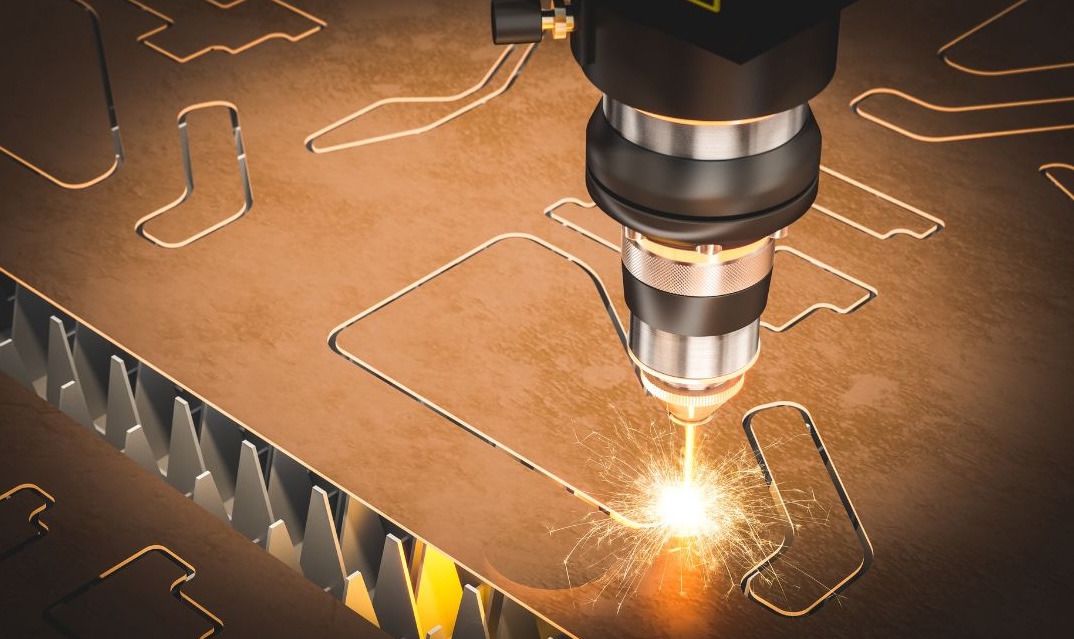
Plasma cutting, developed in the 1950s, uses an electric arc and ionised gas to create a high-temperature plasma jet capable of cutting metal. Plasma-cutting machines use a combination of gas and electricity to produce this plasma, which melts and cuts through metal at high speeds. This technique is effective for cutting through thicker metals, making it popular in industries where speed and thickness are priorities.
Key Differences Between the Two Methods
Laser and plasma cutting differ in their underlying technologies: lasers use focused light, while plasma cutting uses ionised gas and electric arcs. This difference affects various aspects, including energy sources, operating temperatures, and the resulting cut quality. Laser cutting generally requires higher precision and energy consumption, while plasma cutting is suited for rapid cuts on thicker materials. Each technique also varies in safety requirements and ease of use depending on the work environment.
How Laser Cutting Works
Laser Technology Explained
CO₂ and fibre lasers are the two main types used in metal cutting, each with distinct advantages. CO₂ lasers are typically more effective for cutting thicker non-metal materials and metals like mild steel, offering high cut quality. Fiber lasers, on the other hand, excel in cutting reflective metals and thinner materials at faster speeds, with lower maintenance needs. Their high energy efficiency also makes them more cost-effective for certain applications, particularly when working with metals like stainless steel and aluminium.
Materials and Thickness Capabilities
Laser cutting can struggle with highly reflective metals, such as copper and brass, as these materials can reflect the laser beam, potentially causing inefficiencies and even damage to the machine. Advanced fibre lasers have mitigated some of these limitations by offering better absorption rates on reflective materials. However, for very thick, reflective metals, plasma cutting may still be more suitable.
Common Applications of Laser Cutting
Industries like aerospace, automotive, and electronics often rely on laser cutting for its precision and ability to create intricate shapes. This method is especially suited for parts requiring fine details, smooth edges, and minimal post-processing. From custom components to detailed prototypes, laser cutting meets the demands of high-precision applications.
How Plasma Cutting Works
Plasma Technology Explained
This generates a high-temperature plasma jet by using a combination of gas and electricity. When an electric arc passes through a gas (such as nitrogen or oxygen), it becomes ionised, transforming into plasma. This plasma jet reaches extreme temperatures, effectively melting and cutting through metal. The workpiece itself completes the electric circuit, allowing the plasma jet to concentrate on the cutting area.
Materials and Thickness Capabilities
Plasma cutting is highly effective on conductive metals, including mild steel, stainless steel, and aluminium. Compared to laser cutting, plasma is better suited for thicker materials, handling metal thicknesses well beyond the capabilities of most laser cutters. This makes plasma cutting a preferred choice for heavy-duty applications, where material thickness and cutting speed are key factors.
Common Applications of Plasma Cutting
Industries such as construction, shipbuilding, and repair work commonly use plasma cutting for its speed and ability to cut through thicker metals. This method is ideal for heavy-duty projects where rapid cuts are essential, especially in environments where precision is secondary to cutting power and efficiency.
Comparing Precision and Accuracy
Edge Quality and Finish
Laser cutting generally produces a smoother edge quality compared to plasma cutting. The laser beam’s precision results in minimal dross (slag) and a clean, burr-free finish, reducing the need for additional finishing processes. Plasma cutting, while fast and effective for thicker metals, can leave a rougher edge with more dross, especially on thicker materials. Laser cutting tends to be the preferred choice for applications where edge quality and smoothness are priorities.
Tolerances and Detail
Laser cutting is known for working with tight tolerances, making it suitable for intricate designs and detailed work. The narrow laser beam allows for smaller cutting widths, enabling fine, detailed cuts that are challenging for plasma cutters to achieve. Plasma cutting, while effective on thicker metals, has a wider kerf (cutting width) and higher heat input, which can limit its ability to handle complex shapes and fine details without distortion.
Speed and Efficiency in Cutting
Laser Cutting Speed Factors
Cutting speed is influenced by factors such as laser power, material type, and thickness. Generally, lasers cut thinner materials more quickly, while thicker metals require slower, more focused passes to maintain precision. For metals such as stainless steel and aluminium, laser cutting provides an optimal combination of speed and precision, particularly in applications requiring a high-quality finish. On thicker materials, however, the speed advantage diminishes as the laser requires more energy and time.
Plasma Cutting Speed Factors
This method often outpaces laser cutting when dealing with thicker materials. The plasma jet’s intense heat allows for rapid cuts on metals like mild steel and stainless steel. Although plasma cutting is typically less precise than laser cutting, it compensates with faster cutting speeds, particularly on thicker sections where speed is needed more than detailed precision. This makes plasma cutting a practical choice for high-volume or heavy-duty jobs that prioritise speed and thickness capacity.
Cost Considerations
Equipment Costs
Setting up a laser cutting system usually requires a larger initial investment compared to plasma cutting. The complexity of laser machinery, especially high-power lasers like CO₂ and fibre, tends to make them more costly. Plasma-cutting equipment, on the other hand, is generally more affordable and requires less specialised setup, making it accessible for businesses that may have budget constraints.
Operating Costs
While laser cutting systems generally consume more power, particularly with thicker materials, plasma cutting can often be more cost-effective in heavy-duty applications. Plasma cutters are better suited for thicker materials and high-speed cuts, which can result in lower operating costs when cutting large volumes of thick metal. However, for applications requiring high precision and thin metals, laser cutting’s operational costs may be offset by reduced post-processing needs.
Maintenance and Consumables
Maintenance costs for laser systems can be high due to the need for regular replacement of lenses, mirrors, and other sensitive components. Plasma cutters also require consumables, such as nozzles and electrodes, but these tend to be less expensive and easier to replace. Over the long term, plasma cutting can be more economical, especially for applications where ultra-fine precision is not a priority.
When considering cutting options, both offer distinct advantages for metalwork, depending on the project requirements. Laser cutting excels in precision and is ideal for applications where a smooth finish and intricate detail are essential. Plasma cutting is the go-to option for quickly and effectively cutting through thicker metals, especially in heavy-duty settings where speed and material thickness take precedence.
When choosing between the two, it’s advised to consider factors like budget, required accuracy, material type, and thickness. Each method brings unique strengths, and selecting the right technology will ultimately depend on these specific project requirements.
If you’re weighing options for metal fabrication, taking this into account can help you select the best method for your production goals and technical needs.